Today you will have a rough idea of that what is knurling and knurling definition.
The knurled definition is a process to roll patterns of straight, rhombus, or spherical shape into work piece, which can be conducted on manipulative tools or lathes. The reason to create indentations on the knurled parts is for a better grasp than original slippery surface for hands or clamping tool to catch hold of. Generally speaking, The optimal result after knurling depends on the many factors, such as used technique, processed material, dimensions of work pieces and knurling wheel, feed and speed rate, etc. Herein, We’d like to walk you through what is knurling process in 5 points of view in this article that consists of words demanding about 5 minutes of reading time.

Types of patterns
There are knurling patterns that can be roughly categorized into straight, angled, and criss-cross. Among them, the criss-cross type includes rhombic and square these two types, which means 30 degrees and 45 degrees. There are metric and British designs we commonly apply. The value in inches refers to numbers of teeth per inch. While in the metric system they convert to decimal numbers. E.g. 0.3, 0.4, 0.5, 0.6, 0.7, 0.8, 1.0, 1.2, 1.4, 1.6 and so on.
Reference value of spacing between pattern teeth, unit: mm
0.2 | 0.3 | 0.4 | 0.5 |
0.628 | 0.942 | 1.257 | 0.571 |
Specifications of knurling wheel
According to nother diameters, widths and patterns, knurling wheels are divided into specifications.
We’ve got 15, 20, 25 and 30(in mm)as ordinary diameters of knurling wheels and 6, 8, 10, 12, 15, 20 as variant widths.
Form knurling wheel and cut knurling wheel
There are two different types of knurling process: Form knurling and cut knurling.
Form knurling produces surface mainly compressed by non-cutting process. The major difference between cut knurling and form knurling is that there are some sharp edges generated only by cut knurling. We’ve made the following chart to indicate a comparison of their performances.


Cut knurling | Form knurling | |
Material processed | Virtually any material including plastic and cast iron | Cold forming material with thick wall at any position |
Impact on material of work piece | less or no deformation | Increase the outer diameter |
Lathe knurling parameters | Allow higher cutting speed and feed | Slower cutting speed and feed rate |
Impact on lathe | Less pressure on lathe | Apply great pressure on lathe |
Types of Hob
Knurling operation requires a knife handle equipped with a knurling wheel. The knife can be bought directly, or the knurling wheel can be bought and made by oneself.
Generally there are single-wheel, double-wheel and six-wheel.
The single wheel type is to install a flower wheel on a knife handle.
The dual wheel type is a pair of upper and lower flower wheels mounted on a knife handle, usually consisting of two opposite twill wheels.


Six-wheeled is that there are three groups of double wheeled tool holders, which can directly convert different pattern combinations.
Processing and operation precautions of knurling
1. Because when rolling on the lathe the force is quite large, the workpiece must be firmly clamped.
2. Installation of knurling tools should be inclined by 3 to 5 degrees. In this way, the initial contact surface between the roller and the workpiece is narrowed in order to attain a smooth knurling process.
3. The beginning of knurling is a concern, which requires no stopping interpose the initial feed. Only in this way can the workpiece press out the pattern at once. After the pattern is rolled clearly, the wheel proceeds following steps. Otherwise, it is easy to generate breakage on the surface and create a disorderly pattern.
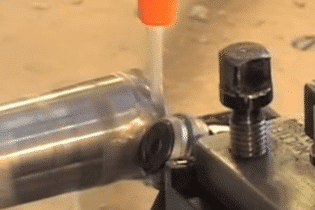
4. When using cut knurling wheel, attention should be paid to the lubrication of the machined surface, so as to avoid the damage of the pattern caused by the accumulation of chips in the groove of the hob during rolling. Roller clearance should not be too large, otherwise radial swing and axial movement will occur.

5. The circumference of the workpiece(π×D) is not necessarily an integral multiple of the knife pitch (t) when rolling a straight line. Otherwise, it may cause the pattern to be scrambled due to the non-coincidence of the rolling tracks after rotation. Then the pressure of rolling ruled lines should be large (the rigidity of machine tool and workpiece is allowed). In order to form deeper and wider lines around the workpiece at the beginning of the second circle, the hob teeth can fall into the groove of the workpiece. Continuous rolling can disperse the misalignment errors into deeper and wider grooves.
6. The machine tool is not easy to run too fast. The general speed is 185 r/min to 230 r/min, and the feed rate is 0.22 mm/r to 0.24 mm/r. Rolling is the same on automatic lathes. When designing the cam, it is required that the knife be cut directly into the prescribed pattern base diameter after the knife contacts the workpiece surface, and then the knife be withdrawn immediately after staying at about 10 ~15. If it is running, let the knife walk horizontally immediately after cutting into the bottom diameter of the pattern. When it reaches the prescribed distance, it should also withdraw the knife immediately. Otherwise, after staying more, it will produce a knife mark and destroy the surface shape of the pattern.
7. Press the net pattern on the automatic lathe, as long as the width of the pattern does not exceed the width of the roller, the net pattern wheel can be rolled directly. If the work piece’s net pattern exceeds the length of the wheel, the compound wheel should be used to walk the pattern.
Hopefully, you have made clear what is knurling and knurled definition. If there is any tip or detail we missed please discuss with us in comment.