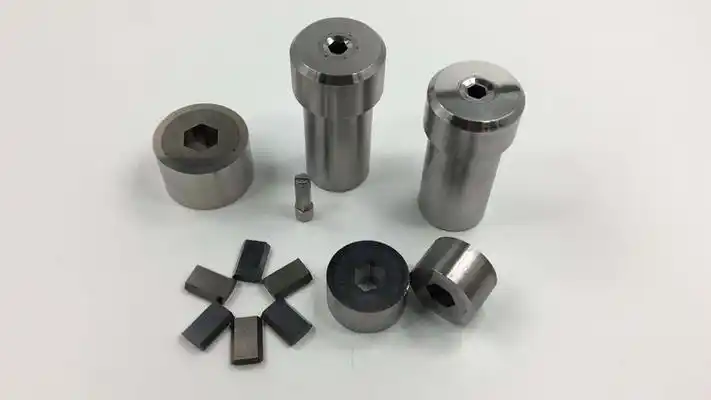
The primary functions of binders in cemented carbide manufacturing
In the powder metallurgy of cemented carbides, binders (also called forming agents) play critical roles, including:
Improving Powder Flowability
Reduces interparticle friction, enabling homogeneous mold filling and uniform compaction.
Prevents powder segregation (e.g., separation of WC and Co).
Enhancing Green Strength
Provides sufficient “green strength” to prevent cracking or edge chipping during handling or demolding.
Minimizes elastic aftereffects (post-compaction expansion).
Lubricating the Mold
Reduces friction between powder and die walls, lowering compaction pressure and extending mold life.
Improves surface finish and minimizes defects (e.g., delamination, cracks).
Facilitating Debinding
Must be fully removable (via thermal decomposition or dissolution) before sintering to avoid carbon residue or impurities that degrade alloy properties.
Performance Requirements for Binders
The binder must possess the following characteristics:
Excellent Compatibility
Uniformly mixes with WC-Co powders without agglomeration or sedimentation.
Chemically inert to powders (e.g., no oxidation of cobalt).
Suitable Melting Point and Viscosity
Melting point must align with compaction temperatures (typically room temperature to 100°C) to ensure:
Liquid-phase homogeneity during mixing.
Solid-phase strength during pressing.
Too high moderate viscosity leads to impedes powder flow.
Too low moderate viscosity leads to insufficient binding force.
High Binding Capacity and Lubricity
Binding capacity: Ensures green strength (flexural strength typically ≥5 MPa).
Lubricity: Reduces compaction pressure (e.g., from 600 MPa to 400 MPa).
Controlled Debinding Behavior
Broad debinding temperature range (e.g., 150–500°C) to prevent cracking from rapid volatilization.
Low carbon residue after debinding (<0.1%) to avoid disrupting alloy carbon balance.
Environmental and Safety Compliance
Non-toxic, low volatility (e.g., water-soluble PEG outperforms solvent-based rubber binders).
Meets industrial emission standards (e.g., sulfur- and chlorine-free).
Cost-Effectiveness
Low-cost and readily available (e.g., paraffin wax is more economical than rubber).
Recyclable or easy to dispose of (e.g., PEG can be water-washed and recovered).
Types of Binder
When manufacturing cemented carbide products, selecting the right binder is crucial for quality and efficiency. Here’s a detailed comparison of the three most common binder types to help you make the best choice for your application.
Paraffin Wax

Characteristics:Composition: Hydrocarbon-based, solid at room temperature with low melting point (50-70°C)
Best for: Small, simple-shaped carbide products
Advantages:
Excellent lubricity reduces die friction
Low debinding temperature (200-400°C) simplifies processing
Cost-effective and readily available
Limitations:
Lower green strength (prone to cracking)
Potential carbon residue during high-temperature debinding
Temperature-sensitive – requires dry storage
Pro Tip: Ideal for mass production of standard inserts where cost is key.
PEG (Polyethylene Glycol)
Characteristics:Composition: Water-soluble polymer with adjustable molecular weight (PEG-2000/4000)
Best for: Complex-shaped tools and precision molds
Advantages:
Higher green strength for intricate shapes
Water-soluble – enables aqueous pre-debinding
Minimal carbon residue
Limitations:
Hygroscopic – requires humidity control
Narrow debinding window (200-300°C)
More expensive than paraffin
Pro Tip: The go-to choice for premium cutting tools requiring precision.
Rubber (SBR, etc.)
Characteristics:Composition: Polymer elastomer requiring organic solvents (e.g., acetone)
Best for: Large, high-density components like rolls and mining tools
Advantages:
Highest green strength
Excellent elasticity prevents cracking
Limitations:
Challenging debinding (500°C+)
Potential sulfur contamination
Environmental concerns with solvents
Highest cost
Pro Tip: Reserved for specialized applications where extreme strength is critical.
Compatibility Principles Between Binders and Wet Milling Media
Paraffin Wax
- Requires organic solvents (e.g., ethanol, acetone)
- Limited solubility in ethanol alone – heating often needed
Recommended Medium: Ethanol + 10-20% acetone (enhances solubility)
PEG (Polyethylene Glycol)
- Excellent water solubility
- Requires oxidation protection for cobalt
Recommended Medium: Deionized water + 0.5% antioxidant (e.g., oxalic acid)
Rubber Binders
- Only soluble in strong organic solvents
Recommended Medium: Pure acetone (requires sealed system to prevent evaporation)
Performance Comparison of Three Major Binder Systems
Binding Strength
Rubber binders provide the highest strength due to their polymer chain structure, making them suitable for large compacts. PEG offers moderate strength ideal for complex geometries, while paraffin wax has the lowest binding strength as it relies solely on physical bonding.
Debinding Process
Paraffin wax can be removed at relatively low temperatures between 200 to 400°C, though carbon balance must be carefully controlled. PEG requires aqueous pre-debinding followed by thermal cycling, but is sensitive to moisture. Rubber binders demand high-temperature pyrolysis above 500°C and carry risks of sulfur contamination.
Residue Effects
Paraffin may leave carbon residues that affect the WC/Co ratio, requiring adjustment of carbon potential during sintering. PEG leaves virtually no residue, making it excellent for high-purity alloys. Rubber can leave sulfur residues that reduce the alloy’s corrosion resistance.
Economic Considerations
Paraffin wax has the lowest initial cost but may incur additional expenses for carbon management. PEG provides the best value for precision components and mass production. Rubber is the most expensive option and is only justified for specialized heavy-duty applications.
Selection Summary
For cost-sensitive production where simple processes are preferred, paraffin wax is suitable but requires careful control of dimensional stability during debinding. When high precision and environmental considerations are priorities, PEG is the optimal choice though it needs humidity-controlled storage. Rubber binders are reserved for applications requiring maximum strength and large components, provided that high-temperature debinding equipment is available.
Modern developments are creating hybrid binder systems that combine the advantages of these materials, such as PEG’s performance with paraffin’s cost benefits through advanced formulation techniques.