Sources of Waste tungsten carbides
Globally, approximately 30,000 to 50,000 metric tons of waste tungsten carbides are generated annually, with China accounting for over 40% of this volume, indicating tremendous recycling potential. Specifically, waste tungsten carbides primarily originate from the following sources:
Residual materials from worn cutting tools, such as lathe tools, milling cutters, and drill bits;
Large tungsten carbide components, including mining drill bits, molds, and rolling mill rolls;
Certain wear-resistant electronic components (e.g., semiconductor packaging materials) that contain tungsten carbides.
Recycling Methods for Waste tungsten carbides
Currently, mainstream recycling technologies include mechanical, chemical, and zinc melting processes, each with its own advantages and limitations:
Crushing Method
The mechanical crushing method is one of the simplest approaches for recycling waste tungsten carbides. It does not alter the chemical composition of the waste material and does not require separation of tungsten and cobalt. After surface cleaning, the waste tungsten carbide undergoes mechanical crushing and ball milling to produce a mixed powder with a chemical composition nearly identical to the original waste (except for a slight increase in iron content and decrease in carbon content).
For tungsten carbides with low cobalt content (which tend to have relatively lower strength), the material can be manually or mechanically crushed to a certain fineness before being ground in a wet mill to achieve the desired particle size for reuse in tungsten carbide production.
Advantages:
Simple process, short workflow
Low energy consumption
Environmentally friendly (no chemical pollution)
Limitations:
Risk of contamination from metal tool debris during manual crushing
Ineffective for high-cobalt tungsten carbides due to their resistance to crushing
Difficulty in ensuring consistent quality for recycled products made from complex carbide mixtures
Advancements in the Crushing Method
Russian researchers have developed an innovative tungsten carbide?recycling process utilizing a simple mechanical crushing approach. This method employs a novel high-power crusher—the conical inertial crusher—enabling high-quality recovery of waste tungsten carbides through crushing and fine grinding alone, without requiring any chemical treatment.
For instance, when processing waste YG6 anvils (used in synthetic diamond production), the waste anvils are first crushed in the conical inertial crusher to produce raw material for tungsten carbide?manufacturing. To enhance the performance of the crushed powder mixture, it is recommended to add 1%–2% cobalt powder, which improves compaction and sintering densification.
Currently, the crushing method continues to evolve, with the adoption of more advanced, cleaner, and efficient crushing equipment for processing waste tungsten carbides.
Zinc Melting Process for tungsten carbide?Treatment
Fundamental Principles of the Zinc Melting Process
The mechanism of the zinc melting process for tungsten carbides is based on the formation of?low-melting-point carbides?between zinc and the binder-phase metals (cobalt or nickel) in tungsten carbides at?900°C. At?896°C, the solubility of cobalt in zinc reaches?27%, allowing the binder metal to separate from the tungsten carbide?and form a?zinc-cobalt solid-solution carbide?liquid. This disrupts the tungsten carbide’s structure, leaving behind a loosely bound?hard-phase skeleton.
Since zinc does not chemically react with refractory metal carbides, and given that zinc’s vapor pressure is significantly higher than cobalt’s at specific temperatures, zinc can be?evaporated and recovered (at 925°C)?for reuse. As a result, the carbide powder obtained through the zinc melting process retains most of its original properties. After the process, cobalt or nickel is extracted into the zinc melt, while the carbides remain. The zinc is then distilled off and recycled for subsequent reuse.
Traditional zinc melting furnaces?are?vertical vacuum furnaces. The system operates under conditions ranging from?vacuum to partial-pressure atmospheres, up to just below atmospheric pressure. The components of zinc melting equipment are illustrated in?Figure 2, while the furnace’s main structure is shown in?Figure 3.
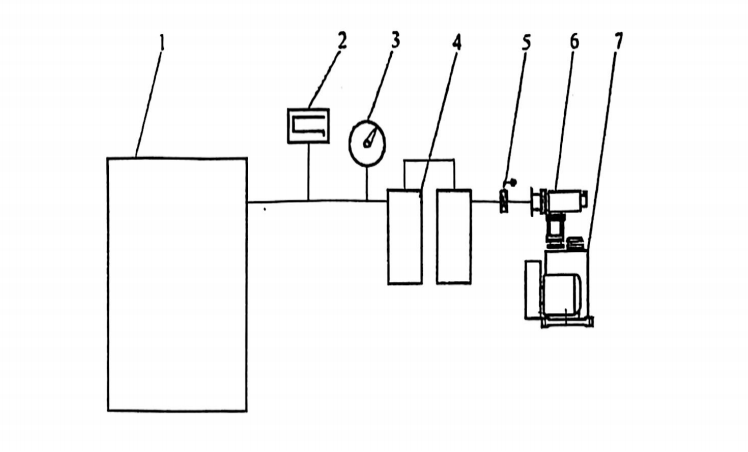
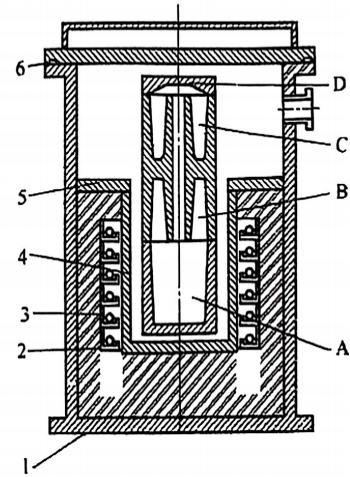
Key Characteristics of the Zinc Melting Process
The zinc melting process was invented by the British in the 1950s. Subsequently, the United States improved this process and enhanced the equipment. After the 1970s, it became widely adopted in many countries. In China, many manufacturers engaged in recycling waste tungsten carbides have mastered this method. Its main advantages are simple process, short flow, simple equipment, small investment, and low cost, making it particularly suitable for processing waste tungsten carbides with cobalt content below 10% and applicable for small enterprises to reuse waste tungsten carbides for carbide reproduction.
However, this process also has some disadvantages. First, the residual zinc content in the mixed material is relatively high. During the zinc melting and zinc recovery processes, whether the equipment is reasonable or not affects the zinc recovery efficiency. Second, the entire process consumes a large amount of electricity, with power consumption for each ton of tungsten carbide reaching approximately 6,000~12,000 kW·h. Additionally, there are environmental protection issues, as zinc emissions may have certain impacts on operators.
Currently, China’s WC-Co carbides have three tungsten carbide grain structures: coarse, medium, and fine. P-type carbides can be roughly divided into three categories based on titanium content: low-titanium, medium-titanium, and high-titanium. During recycling, it is best to strictly separate them to avoid mixing different sizes of tungsten carbide grains or zinc-melted mixed materials with different titanium contents.
Electrochemical Methods
Electrochemical methods mainly include the electrolysis method, as well as the electrolytic electrodeposition method and the electrodialysis electrolysis method developed from the electrolysis method.
Each method offers unique capabilities for metal recovery and purification from tungsten carbide waste streams.
Principle of Electrolysis Method
The electrolysis method involves directly placing waste tungsten carbides into an electrolytic cell with acids (hydrochloric acid, sulfuric acid, nitric acid, etc.) as the electrolyte. During electrolysis, the Co in the carbide transforms into Co2? and enters the solution, while the WC, having lost its binder metal cobalt, becomes a porous carbide. The cobalt-containing solution is precipitated with ammonium oxalate, and cobalt powder is obtained after calcination and reduction. The WC can be directly used in tungsten carbide production after ball milling and crushing or appropriate treatment (such as post-crushing carbon supplementation and re-carburization).
The electrolytic electrodeposition method takes advantage of the fact that hydrogen’s deposition potential is more positive than that of cobalt, causing hydrogen gas to preferentially deposit at the cathode. As the Co2? concentration increases and H? decreases, metallic cobalt is simultaneously deposited alongside hydrogen at the cathode. Thus, the electrolytic system becomes an electrolytic refining process where waste carbide serves as the anode, CoCl? as the electrolyte, and pure cobalt is deposited at the cathode.
The electrodialysis electrolysis method introduces a cation-exchange membrane into the electrolytic cell, dividing it into anode and cathode compartments. The cation-exchange membrane, a functional polymer film selectively permeable to ions, allows only cations to pass while blocking anions. Consequently, Co2? migrates through the membrane into the cathode compartment during electrolysis, while OH? accumulates in the cathode compartment due to the membrane’s barrier effect, raising the pH and resulting in Co(OH)? precipitation. Compared to conventional electrolysis, both the electrolytic electrodeposition and electrodialysis electrolysis methods shorten the cobalt recovery process and improve recovery rates.
High-Temperature Treatment Method
Principle of High-Temperature Treatment
The high-temperature treatment process is a novel recycling technology for tungsten carbides. This method involves re-sintering tungsten carbides at high temperatures to loosen their structure and promote grain growth. Subsequent mechanical crushing yields high-quality powder suitable for producing coarse-grained tungsten carbides. tungsten carbides manufactured from this powder exhibit performance metrics that meet or exceed those of standard carbide products. The high-temperature treatment process provides a new approach for recycling waste tungsten carbides and producing coarse-grained tungsten carbides.
High-Temperature Treatment Process for Waste tungsten carbides
The high-temperature treatment of tungsten carbides is conducted in specially designed high-temperature furnaces. Under a protective atmosphere at temperatures exceeding 1800°C, the waste carbide undergoes treatment where binder metals like cobalt liquefy and boil, causing carbide deformation and significant volume expansion. The carbide structure transforms into a porous, honeycomb-like formation, making the hardened carbide extremely easy to crush and process. During this high-temperature treatment:
A substantial liquid phase forms in the carbide
Atomic diffusion intensifies→
WC dissolution-precipitation effects strengthen→
WC grains grow rapidly from 1-2μm to several dozen or even hundreds of micrometers→
Defects in WC crystal structures are eliminated during recrystallization→
WC crystal structures become more complete→
Trace metal/non-metal impurities and harmful contaminants are removed
Characteristics of High-Temperature Method and Regenerated carbide Performance
This regenerated mixed material is particularly suitable for producing coarse-grained, high-cobalt-content tungsten carbides. For fine-grained, low-cobalt carbides:
- Higher treatment temperatures are required to generate sufficient stress for expansion and porosity
- Modified preparation and sintering processes are necessary for medium-fine grain production
Processing steps:
Initial crushing of treated carbide
Ball milling to -180 mesh (80μm) for regeneration suitability
The recycled carbide powder is ideal for coarse-grained tungsten carbide production. Test results show:
- Physical-mechanical properties match those of virgin powder carbides
- Grain size increases by 1μm
- Service life of rock drilling buttons and cold heading dies improves by 20%
Advantages:
- Short process flow
- Simple equipment requirements
- Clean recycled mixed materials
- Low environmental pollution
- High recovery rates
Limitations:
- High energy consumption
- Some cobalt loss during high-temperature processing
- Recycled material only suitable for coarse carbide grain carbides
Currently used by manufacturers in industrialized nations like Japan and Sweden.
Conclusion
Waste tungsten carbide recycling represents not just economic resource reuse but a crucial component of green manufacturing. With advancing technology and policy support, the recycling industry will become more efficient and environmentally friendly, contributing to global sustainable development.
What’s more, industrial enterprises should establish classified recycling systems.Individual users should properly dispose of used tools/drill bits through professional recyclers
“Waste is just resources in the wrong place” – tungsten carbide recycling perfectly embodies this philosophy!