When applied correctly, surface treatments can improve both the physical properties and functionality of machined parts. Since different types of CNC machining surface finishes involve distinct procedures and outcomes, understanding the fundamentals of these treatments is essential to determine the best option that meets the requirements of your intended application.
Why Do Machined Parts Require Surface Finishing?
CNC machining processes (including milling and turning) often leave visible cutting marks, which can compromise the surface quality of machined parts. Although CNC machining delivers precision components, these parts frequently require surface finishing for various reasons.
Why Surface Finishing Is Crucial for CNC-Machined Metal Parts:
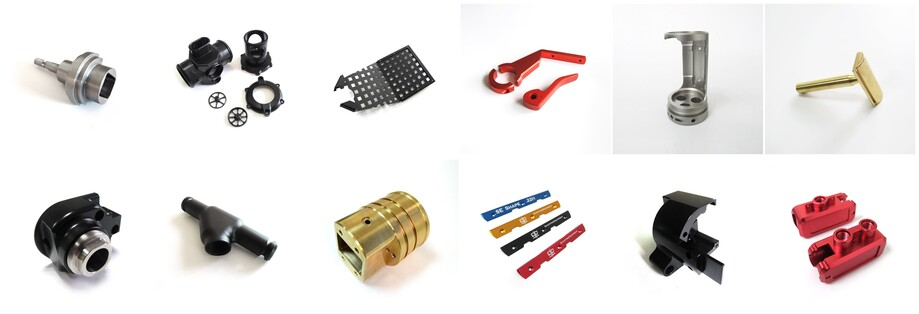
Enhancing Appearance
Surface treatments such as sanding, polishing, electroplating, or painting help conceal sharp edges and machining marks left during CNC processing. As a result, these finishes enhance the visual appeal of CNC-machined parts.
Improving Corrosion Resistance
Most CNC-machined materials are susceptible to corrosive substances. To protect the surface of machined components and extend their service life, product designers often employ surface treatments like anodizing, polishing, and passivation.
Ensuring Hygiene & Cleanliness
Manufacturers apply various surface finishes to CNC-machined parts to ensure they are easy to clean and maintain. This is particularly critical in applications where hygiene is paramount, such as food processing equipment and medical devices.
Optimizing Functional Performance
Different CNC surface treatments are used to enhance material properties (e.g., conductivity), reduce friction, and add other desirable characteristics—improving overall functional performance.
Customization Options
By selecting the appropriate surface finish for your machined parts, you can customize them to meet specific preferences and requirements. A variety of finishes can be achieved to deliver desired surface properties, textures, or colors.
Common Types of Surface Finishes
Different surface treatments are suitable for various CNC machining materials, each with distinct surface roughness values. However, it is crucial to select the surface finish that best ensures optimal performance, functionality, durability, and visual appeal of the machined parts.
Below are the commonly used surface finishes for metal CNC-machined parts:
研磨
Polishing is a classic mechanical finishing process that uses chemical agents or abrasives to create a highly glossy, mirror-like surface on metal parts. This finishing technique enhances the physical properties of machined metal components, improves corrosion resistance, ensures better cleanliness, and reduces friction.
Polishing is particularly suitable for metals such as aluminum, stainless steel, and brass. It is widely adopted by product designers and manufacturers in the food processing, medical, and luxury goods industries due to its functional and aesthetic benefits.
Although polishing can produce a smooth, reflective surface that enhances visual appeal, the process can be time-consuming and labor-intensive. This is especially true for machined parts requiring extremely high finishes or those with complex geometries.
Electroplating
Electroplating is a finishing process that involves depositing a layer of metal coating onto machined parts to increase their thickness. Applying this surface treatment to CNC-machined components protects them from corrosion, impact, high temperatures, and rust, ensuring long-term durability. This process is most suitable for metals such as chromium, cadmium, tin, copper, nickel, and gold. Electroplating enhances adhesion between the substrate and its external coating while also enabling machined parts to acquire magnetic or conductive properties depending on the plated metal.
Unlike other CNC surface treatments, electroplating is not environmentally friendly due to its generation of hazardous waste. Improper handling can lead to significant pollution. Additionally, electroplating is time-consuming and relatively expensive, requiring specialized equipment, metals, and chemicals—especially when multiple layers are needed on metal components.
Passivation
Passivation protects ferrous materials like steel and stainless steel from corrosion and rust, improving appearance, performance, and cleanliness. This chemical treatment involves immersing machined metal parts in acidic solutions such as nitric or citric acid to remove surface iron, resulting in a smooth, polished finish.
Since passivation is not a coating, it does not require masking or add thickness to the machined part. The acid bath eliminates traces of iron and rust from the surface, forming a protective layer composed of chromium or nickel. While nitric acid is the traditional choice for passivation, citric acid baths have gained widespread acceptance due to their shorter processing times.
Passivated parts exhibit excellent rust resistance, making them ideal for outdoor applications. Moreover, passivation is widely used across industries—from aerospace (requiring high-quality steel and tight tolerances) to medical sectors (where sterilization and longevity are critical).
However, passivation may extend production lead times because machined metal parts must undergo pretreatment, such as cleaning to remove debris, grease, or other contaminants. While immersion is the most common passivation technique (offering faster cycles and better consistency), acid spraying serves as a viable alternative.
Anodizing
Anodizing creates a protective oxide layer on the surface of machined metal parts. This coating shields the metal from corrosion and wear while being compatible with various colors. It is non-conductive and highly durable (Type III). Anodizing is ideal for forming corrosion-resistant coatings on aluminum and titanium components.
To anodize a CNC-machined metal part, it is immersed in a diluted sulfuric acid solution, and an electrical current is applied between the part (anode) and a cathode. This triggers an electrochemical reaction, converting the exposed surface into hard titanium or aluminum oxide. However, critical features like threaded holes—which must remain conductive—should be masked before anodizing.
Anodized parts can be dyed in colors such as gold, red, black, or blue before sealing. The coating’s thickness and density can be adjusted by varying the anodizing time, consistency, and duration. There are three primary anodizing variants, each with distinct processes, coating thicknesses, and properties:
Type I (Chromic Acid Anodizing)
Produces the thinnest layer, preserving part dimensions.
Results in a grayish finish that cannot be dyed.
Type II (Boric-Sulfuric Acid Anodizing)
A safer option with better paint adhesion, allowing for color customization.
Known as “decorative” or standard anodizing, with coatings up to 25 μm thick.
Type III (Hardcoat Sulfuric Acid Anodizing)
The most common type, especially for aluminum and titanium alloys.
Provides the clearest surface, enabling the widest color compatibility.
Coating thickness ranges from 0.001 to 0.004 inches (25–100 μm).
Combined with PTFE/Teflon, it forms a dry lubricated surface.
Alodine
Alodine or chem film is the brand name for chromate conversion coating. This chemical surface treatment requires immersing machined components in a proprietary chemical solution primarily composed of chromium. When selecting Alodine treatment for metal CNC machined parts, please ensure the process complies with the MIL-DTL-5541F standard. This standard specifies the technical requirements for chemical conversion coatings on aluminum and aluminum alloys in U.S. military specifications.
The Alodine protective coating effectively inhibits corrosion. More importantly, it can be used in conjunction with decorative surface treatments as it significantly improves the adhesion of paints and adhesives. Unlike other surface treatments that reduce the thermal and electrical conductivity of aluminum parts, Alodine actually enhances the electrical conductivity of aluminum components. This surface treatment method is relatively low-cost, but its coating is more prone to scratches and surface damage.
コーティング
Powder coating is an electrostatic process that applies dry powder to form a thin, uniform protective layer on the surface of CNC-machined parts. This technique is compatible with all metals and enhances the strength, corrosion resistance, and wear resistance of the components.
Unlike anodized metal parts, powder-coated metal parts exhibit superior impact resistance and are available in a wide range of colors. The process can be combined with sandblasting to produce machined parts with smooth, uniform surfaces and exceptional corrosion resistance. The powders used can be either thermosetting or thermoplastic polymers.
Although similar to painting, powder coating involves applying dry powder to the metal part surface and curing it in an oven. For optimal corrosion protection, machined parts may first require a primer treatment, such as chromate conversion or phosphating. The parts are then coated with dry powder using an electrostatic spray gun and cured in an oven at 200°C (392°F). Multiple layers can be applied to achieve the desired coating thickness, typically ranging from 18 μm to 72 μm.
Electroplating
Electroplating is a finishing process that deposits a metallic coating onto machined metal parts to increase their thickness. This surface treatment enhances CNC-machined components by protecting them against corrosion, impact, high temperatures, and rust, significantly extending their service life. The process is most suitable for metals such as chromium, cadmium, tin, copper, nickel, and gold. Electroplating improves adhesion between the substrate and external coatings while also enabling customized properties—magnetic or conductive—depending on the plated metal.
Unlike other CNC surface treatments, electroplating is not environmentally friendly due to its generation of hazardous waste. Improper disposal can lead to severe pollution. Additionally, the process is time-consuming and relatively costly, requiring specialized equipment, metals, and chemicals—especially for multi-layer plating.
Passivation
Passivation protects ferrous materials (e.g., steel, stainless steel) from corrosion and rust, improving appearance, performance, and cleanliness. This chemical treatment involves immersing machined parts in acidic solutions (nitric or citric acid) to remove surface iron, resulting in a smooth, polished finish.
As passivation is not a coating, it requires no masking and adds no thickness to the part. The acid bath eliminates iron and rust residues, forming a protective chromium/nickel oxide layer. While nitric acid is the traditional choice, citric acid baths are now widely adopted for their shorter cycle times.
Passivated parts excel in rust resistance, making them ideal for outdoor applications. The process is critical across industries—from aerospace (demanding high-grade steel and tight tolerances) to medical (requiring sterilization-compatible surfaces).
However, passivation may extend lead times due to mandatory pre-treatment (e.g., cleaning to remove debris or oils). Immersion remains the most common method for its consistency, though acid spraying offers an efficient alternative for complex geometries.
Electroless Nickel Plating
The electroless nickel plating process involves forming a nickel alloy protective layer on CNC machined parts to enhance their corrosion resistance. It uses a nickel bath and chemical reducing agents (such as sodium hypophosphite) to deposit a nickel alloy coating (typically nickel-phosphorus) on metal components. This process uniformly applies the nickel alloy coating to complex parts with features like holes and grooves.
There are several types of electroless nickel plating, each with different phosphorus contents. These include low-phosphorus, medium-phosphorus, and high-phosphorus nickel.
Parts treated with nickel plating typically exhibit excellent hardness and wear resistance. Additionally, they can be made harder through heat treatment. The electroless nickel plating process is suitable for various metals, including stainless steel, aluminum, and steel.
Despite its significant advantages, this method has certain limitations, including:
Subsequent reduction in plating rate
Accumulation of contaminants in the nickel bath
Increasing phosphorus content
Furthermore, electroless nickel plating is less suitable for rough, uneven, or poorly machined surfaces.
Metal CNC machined parts can undergo any surface treatment to ensure they meet your project requirements. In this article, we have discussed the most common surface treatments for metal CNC parts, each with its unique advantages and disadvantages. We hope this helps you understand how these surface treatments work and their outcomes, enabling you to determine the most suitable surface treatment for your specific application.