fロム 原材料 に 最終製品
炭化タングステンは一般に「カーバイド」と呼ばれ、店頭でよく使われる素材です。このタングステンとカーボンの化合物は、過去數(shù)十年で金屬切削の世界を完全に変え、速度と送り速度を向上させ、工具壽命を延長しました。タングステンカーバイドは 1925 年に工具材料として初めて研究されました。その後、Ge はタングステンカーバイド切削工具を製造するための特別部門を設立しました。 1930 年代後半、ケナメタルの創(chuàng)設者であるフィリップ M. マッケンナは、混合物にチタン化合物を添加すると、工具が高速でより良く機能する可能性があることを発見しました。これは今日の電光石火の切斷速度に向けて動き始めました。
工具や刃物を構成する材料である「超硬合金」は、実際には炭化タングステンの粒子を他の材料とともに結合剤として金屬コバルトで固めたものです。
始まり 地中に
採掘、タングステンへの精製、または炭化タングステンへの製造が可能なタングステン鉱石がいくつかあります。ウルフラマイトが最も有名です。鉱石は粉砕され、加熱され、化學処理されて酸化タングステンになります。
次に、微細な酸化タングステンを浸炭して炭化タングステンとする。 1つの方法では、酸化タングステンをグラファイト(炭素)と混合する?;旌衔铯?1200 ° C(2200 ° F)に加熱すると、化學反応が発生して酸化物から酸素が除去され、炭素とタングステンが結合して炭化タングステンが形成されます。
粒子サイズが特性を定義する
炭化物粒子のサイズによって、最終製品の機械的特性が決まります。粒子サイズは、酸化タングステン粒子のサイズと、酸化物/炭素混合物を処理する時間と溫度によって異なります。
炭化タングステンの粒子は砂粒ほどの大きさです。サイズは 0.5 ミクロンから 10 ミクロンの範囲です。一連のふるいは、1 ミクロン未満、1.5 ミクロンなどのさまざまな粒子サイズを選別します。
この時點で、炭化タングステンを「グレードパウダー」に混合する準備が整います。タングステンカーバイド業(yè)界では、合金ではなくグレードについて話しますが、それは同じ意味です。
炭化タングステンは、このグレードの他の成分と一緒に混合容器に入ります。粉末狀のコバルト金屬は、材料を結合する「接著剤」として機能します。切削時の材料特性を向上させるために、炭化チタン、炭化タンタル、炭化ニオブなどの他の材料が追加されます。これらの添加剤を使用しないと、鉄系材料を切削する際に、特に高速切削において、炭化タングステン工具が工具とワークピースの破片との間で化學反応を起こし、工具內にピットが殘る可能性があります。
混ぜあわせる

これらの成分はすべて、アルコールやヘキサンなどの液體と混合され、混合容器、多くの場合ボールミルと呼ばれる回転ドラムに入れられます。グレードの成分に加えて、コバルトを炭化物粒子に付著させるプロセスを助けるために、直徑 1/4 インチから 5/8 インチの超硬ボールが追加されます。ボールミルは、直徑 5 インチ、長さ 5 インチ程度の小さいものから、55 ガロンのドラムと同じくらい大きい場合もあります。
混合が完了したら、液體を除去する必要があります。これは通常、ステンレス鋼のサイロのように見えるスプレー乾燥機で発生します。不活性乾燥ガス、窒素またはアルゴンが下から上に吹き込まれます。すべての液體を除去すると、殘った乾燥した物質は砂のように見える「グレードパウダー」です。
カッターインサートの場合、グレードパウダーは、プロセスの後半で起こる収縮を考慮して特別に設計されたインサート形狀の金型に入れられます。醫(yī)薬品の錠剤を形成する方法と同様のプロセスで、粉末を金型に圧縮します。
焼結
材料の要求特性を得るために、粉末成形體を一定の溫度(焼結溫度)まで加熱し、一定時間保持した後、冷卻することを焼結といいます。焼結の過程では、原子移動による加熱により粒子間の結合が実現(xiàn)します。粒子が結合すると焼結體の強度が増し、多くの場合密度が増加します。
インサートを爐から取り出して冷卻すると、緻密で硬くなります。品質管理チェックの後、インサートは通常、正しい寸法と切れ刃を実現(xiàn)するために研磨またはホーニング加工されます。半徑 0.001 インチのホーニングが一般的ですが、部品によっては 0.5 千分の 1 または 0.002 インチもの刃先半徑が與えられ、一部は焼結されたまま「非常に鋭い」ままになります。
一部のタイプとデザインのインサートは、正しい刃先を備えた最終形狀で仕様どおりに焼結爐から出てくるため、研削やその他の操作は必要ありません。
超硬ソリッド工具のブランクの製造プロセスは非常に似ています。グレードの粉末をプレスして成形し、その後焼結します。ブランクまたはストックは、顧客に出荷する前に後で適切なサイズに研磨することができ、顧客は研削またはおそらく EDM によってそれを成形します。
ほとんどの非鉄用途向けのインサートは、この時點で梱包して出荷する準備ができている可能性があります。鉄金屬、高溫合金、チタンの切斷を目的としたものは、コーティングする必要があります。
cオーティング シーンをドロップする
困難な切削條件下で工具壽命を延ばすために、多くの種類と組み合わせのコーティングが開発されています。これらは、化學蒸著 (CVD) または物理蒸著 (PVD) という 2 つの方法で適用できます。どちらのタイプも爐に適用されます。
化學蒸著
CVD の場合、コーティングの厚さは通常 5 ~ 20 ミクロンです。フライス加工および穴あけブレードは、通常、5 ~ 8 ミクロンの硬度に達します。これらの操作では、より優(yōu)れた表面仕上げとより大きな衝撃が必要となり、より高い刃先の靭性が必要となるためです。旋削加工の場合、コーティングは 8 ~ 20 ミクロンの範囲にあることがよくあります。コーナリング時には、熱と摩耗の方が心配になることがよくあります。
ほとんどの CVD コーティングは複數(shù)の層、通常は 3 層で構成されています。
各社は獨自のコーティング「配合」を持っています。これは典型的なスキームであり、3 つのレイヤーで構成されます。
? 硬度と耐摩耗性を備えた炭化チタンの層
? アルミナの層。高溫でも硬度を維持し、非常に安定した化學的特性を持ちます。
? 工具に溶接されたワークピースの破片によって引き起こされる金屬の蓄積を防ぐ窒化チタンの層。このコーティングは金色で、エッジの磨耗が容易に観察されます。 CVD コーティングを適用するには、部品をパレットに置き、爐內に密封します。爐を排気した。
物理蒸著
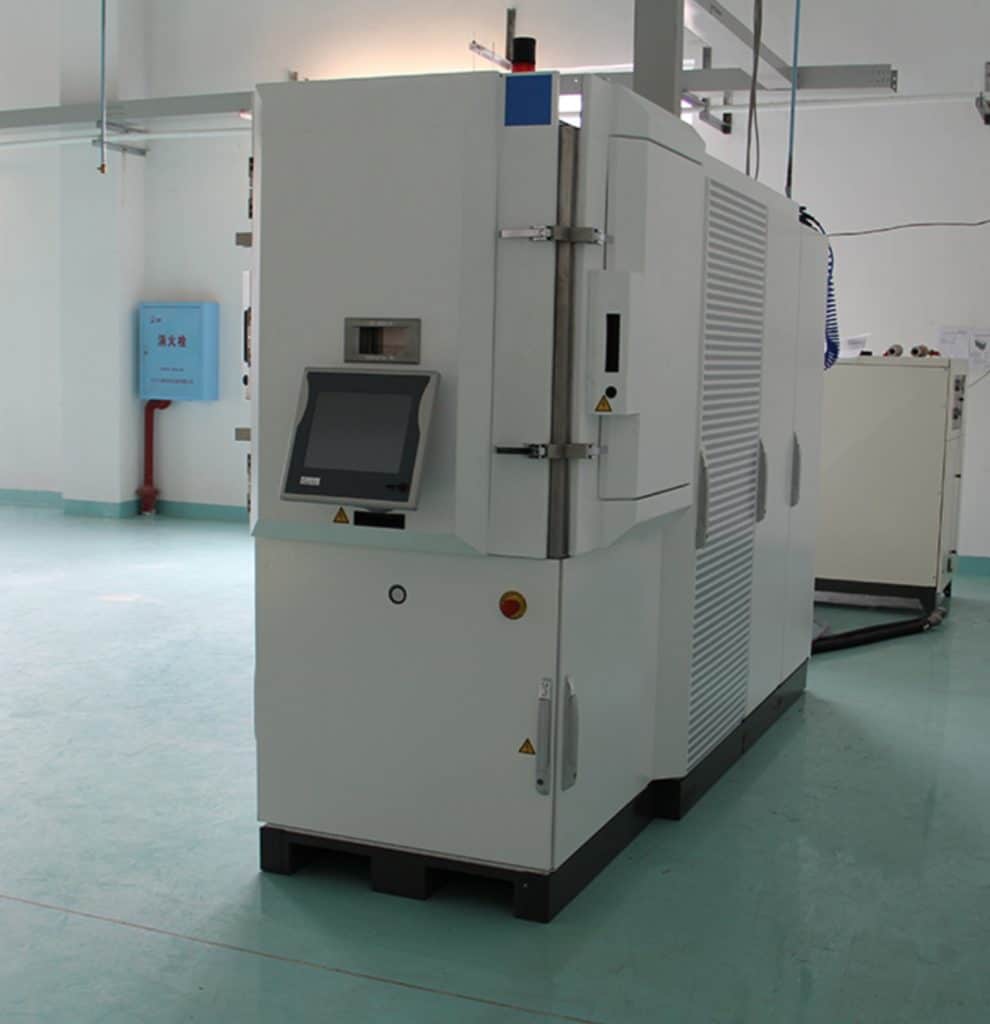
PVD コーティングの厚さは通常約 2 ~ 4 ミクロンです。メーカーが異なれば、使用するレイヤーも異なります。これらの PVD コーティングは、高溫のニッケル ベース、コバルト ベース、チタン ベースの材料、場合によっては鋼やステンレス鋼の切斷に非常に適しています。
炭窒化チタン、窒化チタン、窒化チタンアルミニウムは PVD コーティングとして広く使用されています。後者は、化學的安定性が最も高く、最も硬い PVD コーティングです。
インサートは、互いに分離されるようにフレームに取り付けられます。各ラックが回転し、ラック アセンブリ全體が爐內で回転するため、インサートの各表面が蒸著プロセスにさらされます。ストーブは空になった。
プラグインには強いマイナスの電荷がかかります。チタン片、またはチタンとアルミニウムを爐の壁または床に取り付けます。金屬はアークまたは電子ビームを通じて蒸発し、正に帯電した金屬イオンを放出します。これらのイオンは、負に帯電したインサートによって引き寄せられます。窒素とメタンを適切に添加して、さまざまな種類のコーティングを実現(xiàn)します。
インサートを爐から取り出した後、再度研磨するか、梱包して直接出荷することができます。
タングステンカーバイド工具の設計を継続的に改善し、より優(yōu)れたコーティング技術を開発することで、工具メーカーは送り速度と速度の向上というプレッシャーに加え、工具壽命の延長とコスト削減の必要性に対処しています。