The fatigue strength of metal materials is very sensitive to various external and internal factors. External factors include the shape and size of the part, surface finish and service conditions, while internal factors include the composition of the material itself, organizational state, purity and residual stress. Subtle changes of these factors will cause fluctuations or even large changes in the fatigue properties of materials.
The influence of various factors on fatigue strength is an important aspect of fatigue research. This research will provide a basis for the reasonable structural design of parts, the correct selection of materials and the rational formulation of various cold and hot machining processes, so as to ensure the high fatigue performance of parts.
effect on fatigue of stress concentration
The conventional fatigue strength is measured by carefully machined smooth specimens. However, the actual mechanical parts inevitably have different forms of notches, such as steps, keyways, threads and oil holes. The existence of these notches causes stress concentration, so that the maximum actual stress at the root of the notch is much greater than the nominal stress borne by the part, and the fatigue failure of the part often starts from here.
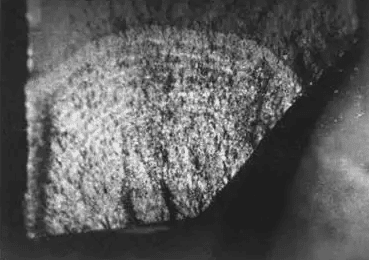
Influence of size factor
Due to the inhomogeneity of the material structure and the existence of internal defects, the increase of the size will increase the failure probability of the material, thus reducing the fatigue limit of the material. The existence of size effect is an important problem in applying the fatigue data measured by small samples in the laboratory to large-scale actual parts. Because it is impossible to reproduce the stress concentration and stress gradient on the actual size parts on the small samples, the laboratory results are disconnected from the fatigue failure of some specific parts.
Influence on fatigue of surface processing state
There are always uneven machining marks on the machined surface, which are equivalent to tiny notches, causing stress concentration on the material surface, thus reducing the fatigue strength of the material. The test shows that for steel and aluminum alloy, the fatigue limit of rough machining (rough turning) is reduced by 10% – 20% or more than that of longitudinal fine polishing. The higher the strength of the material, the more sensitive it is to the surface finish.
Effect of chemical composition
There is a close relationship between the fatigue strength and tensile strength of materials under certain conditions. Therefore, under certain conditions, any alloy element that can improve the tensile strength can improve the fatigue strength of materials. Comparatively speaking, carbon is the most important factor affecting the strength of materials. However, some impurity elements which form inclusions in steel have adverse effects on fatigue strength.
Effect on fatigue of heat treatment and microstructure
Different heat treatment conditions will result in different microstructures. Therefore, the effect of heat treatment on fatigue strength is essentially the effect of microstructure. Although the same static strength can be obtained for materials with the same composition due to different heat treatment, the fatigue strength can vary in a considerable range due to different structures.
At the same strength level, the fatigue strength of flake pearlite is obviously lower than that of granular pearlite. The finer the cementite particles, the higher the fatigue strength.
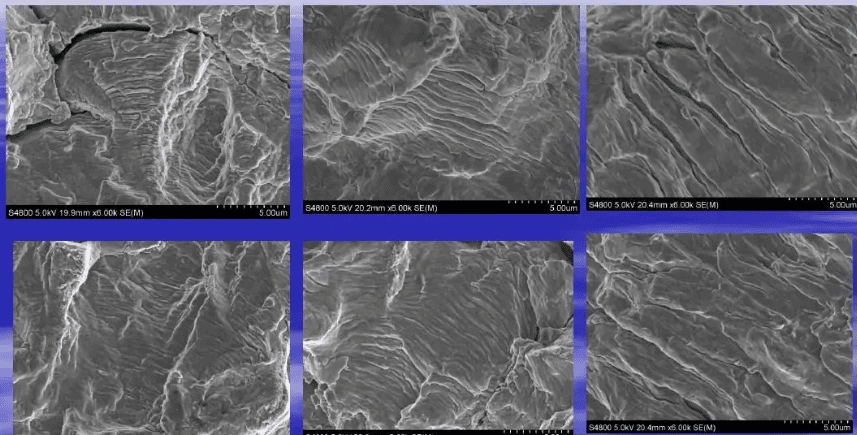
Effect of inclusions
The inclusion itself or the holes generated by it are equivalent to tiny notches, which will produce stress concentration and strain concentration under the action of alternating load, and become the crack source of fatigue fracture, causing adverse effects on the fatigue properties of materials. The influence of inclusions on fatigue strength depends not only on the type, nature, shape, size, quantity and distribution of inclusions, but also on the strength level of materials, the level and state of applied stress.
Different types of inclusions have different mechanical and physical properties, different properties from base metal, and different effects on fatigue properties. Generally speaking, plastic inclusions (such as sulfides) that are easy to deform have little effect on the fatigue properties of steel, while brittle inclusions (such as oxides, silicates, etc.) do great harm.
Inclusions with larger expansion coefficient than the matrix (such as sulfide) have less influence due to compressive stress in the matrix, while inclusions with smaller expansion coefficient than the matrix (such as alumina) have greater influence due to tensile stress in the matrix.
The compactness of inclusion and base metal also affects the fatigue strength. Sulfide is easy to deform and closely bond with the base metal, while oxide is easy to separate from the base metal, resulting in stress concentration. Therefore, from the type of inclusions, sulfide has little effect, while oxides, nitrides and silicates are more harmful.
Effect of surface property change and residual stress
In addition to the surface finish mentioned above, the influence of surface state also includes the change of surface mechanical properties and the influence of residual stress on fatigue strength. The change of surface mechanical properties can be caused by the difference of surface chemical composition and structure, or by deformation strengthening.
Surface heat treatment such as carburizing, nitriding and carbonitriding can not only increase the wear resistance of parts, but also improve the fatigue strength of parts, especially an effective means to improve the corrosion fatigue and biting corrosion resistance.
The influence of surface chemical heat treatment on fatigue strength mainly depends on loading mode, carbon and nitrogen concentration in the carburized layer, surface hardness and gradient, the ratio of surface hardness to core hardness, layer depth, and the size and distribution of residual compressive stress formed by surface treatment. A large number of tests show that as long as the notch is machined first and then treated by chemical heat treatment, generally speaking, the sharper the notch is, the more the fatigue strength will be improved.
The effect of surface treatment on fatigue performance is different under different loading modes. Under axial loading, the stress in the surface layer is the same as that under the layer because there is no uneven distribution of stress along the layer depth. In this case, the surface treatment can only improve the fatigue performance of the surface layer. Because the core material is not strengthened, the improvement of fatigue strength is limited. Under bending and torsion conditions, the stress distribution is concentrated in the surface layer. The residual stress formed by surface treatment and this additional stress are superimposed to reduce the actual stress on the surface. At the same time, due to the strengthening of surface materials, the fatigue strength under bending and torsion conditions can be effectively improved.