張力は簡単な機械的特性試験です。テストゲージの距離內では、応力は均一であり、応力、ひずみ、および性能指標の測定は安定しており、信頼性が高く、理論計算に便利です。引張試験を通じて、弾性変形、塑性変形、および破壊の過程における最も基本的な機械的特性指標、たとえば正の弾性率 E および降伏強度 σ 0.2 を測定できます。降伏點 σ s。引張強さ σ b.破斷後の伸び率 δ および絞り値 ψ など 引張試験で得られる機械的特性指標 e σ 0.2、 σ s、 σ b、 δ、ψ などは、材料固有の基本特性であり、主な根拠となります。工學設計で。
金屬の塑性変形と引張強度の関係
ほとんどの金屬材料では、弾性変形領域では応力とひずみが比例します。応力または歪みが増加し続けると、ある時點で、歪みは加えられた応力に比例しなくなります。
この時點で、隣接する最初の原子との結合が壊れ始め、新しい原子グループで変更されます。これが起こると、応力が除去された後、材料は元の狀態(tài)に戻らず、つまり、変形は永続的で回復不能になり、材料は塑性変形ゾーンに入ります(図1)。
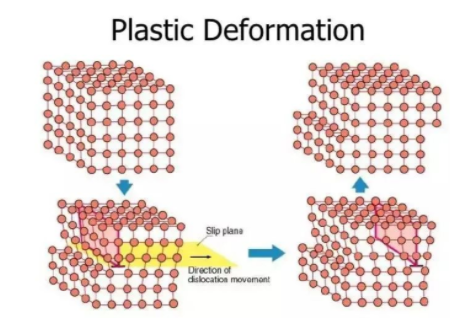
実際、材料が弾性ゾーンから塑性ゾーンに変化する正確なポイントを特定することは困難です。図 2 に示すように、ひずみが 0.002 の平行線が引かれます。応力-ひずみ曲線はこの線で切斷され、降伏応力が降伏強度として決定されます。降伏強度は、大きな塑性変形が発生する応力に等しくなります。ほとんどの材料は均一ではなく、完璧な理想的な材料でもありません。材料の歩留まりは、通常は加工硬化を伴うプロセスであるため、特定のポイントではありません。
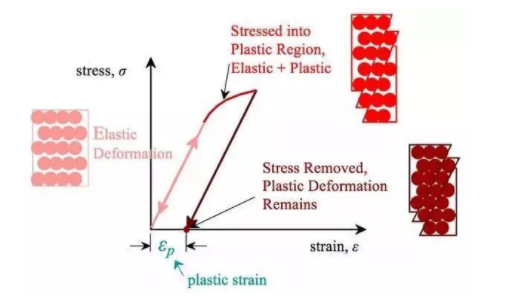
ほとんどの金屬材料の場合、応力-ひずみ曲線は図 3 に示す曲線と似ています。負荷が始まると、応力はゼロから増加し、ひずみは直線的に増加します。材料が降伏するまで、曲線は直線性から逸脫し始めます。
応力を増やし続けると、曲線は最大値に達します。最大値は、曲線の最大応力値である引張強度に対応し、図では m で表されます。破斷點とは、材料が最終的に破斷する點であり、図では F で示されています。
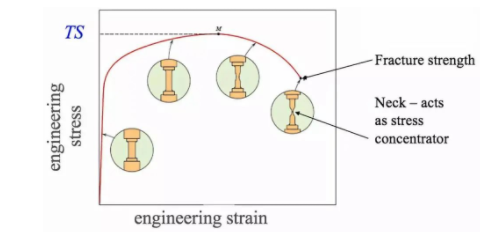
典型的な応力-ひずみ試験裝置と試験サンプルの形狀を図 4 に示します。引張試験中、サンプルはゆっくりと引っ張られ、長さと加えられた力の変化が記録されます。力変位曲線が記録されます。応力-ひずみ曲線は、サンプルの元の長さ、ゲージ長、および斷面積を使用して描くことができます。
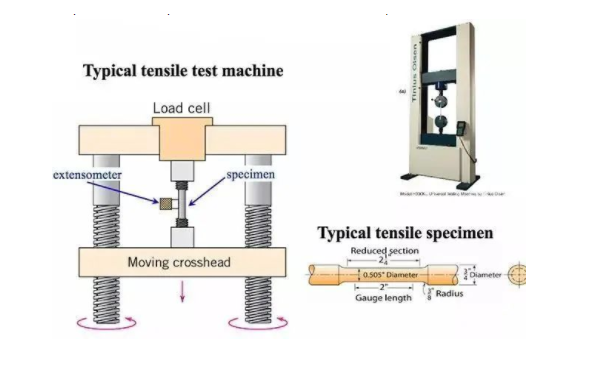
図 4 応力ひずみ試験
引張塑性変形を受ける可能性のある材料の場合、2 種類の曲線が最も一般的に使用されます。エンジニアリング応力 - エンジニアリングひずみ曲線と真の応力 - ひずみ曲線です。それらの違いは、応力の計算に使用される領域が異なることです。前者はサンプルの初期面積を使用し、後者は引張プロセス中のリアルタイム斷面積を使用します。したがって、応力-ひずみ曲線では、真の応力は一般に工學的応力よりも高くなります。
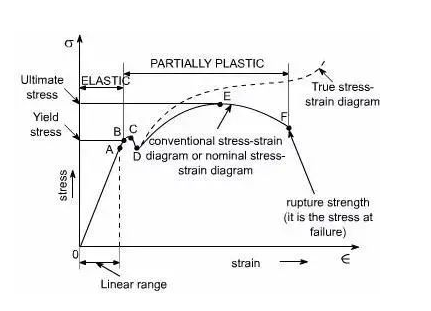
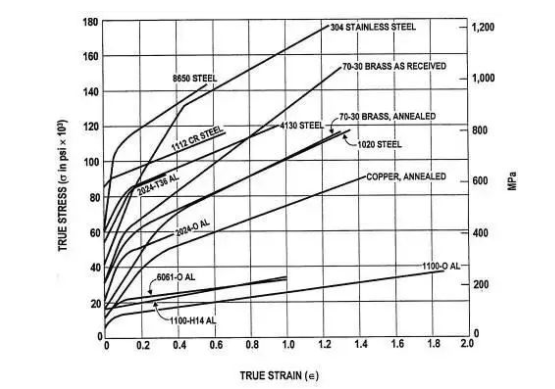
図 6 さまざまな実際の金屬材料の真の応力と真のひずみ曲線
最も一般的な引張曲線には 2 種類あります。1 つは明らかな降伏點を持つ引張曲線です。第二に、明らかな降伏點のない引張曲線。降伏點は、最初の塑性変形に対する金屬の抵抗を表します。これは、工學技術において最も重要な機械的特性の 1 つです。
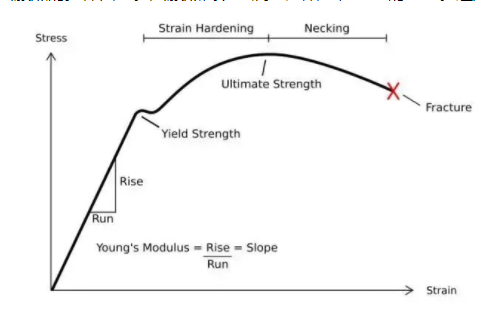
金屬の塑性変形から引張強度を測定するには?
殘留塑性変形は重要な基礎です。一般に、エンジニアリングメタルに一定の殘留塑性変形を人為的に加えたときの抵抗力を降伏強度といい、條件付き降伏強度とも呼ばれます。つまり、明らかな塑性降伏點はなく、明らかな降伏強度もありません。実際の金屬の耐力を知りたい場合は、判定條件が必要になるため、條件付耐力があります。金屬成分が異なれば、條件付耐力に対応する殘留変形量も異なります。一部の過酷な金屬コンポーネントの場合、殘留変形は小さいはずですが、通常の金屬コンポーネントの対応する殘留変形は、條件下で降伏したときに大きくなります。一般的に使用される殘留変形は、0.01%、0.05%、0.1%、0.2%、0.5%、および 1.0% です。
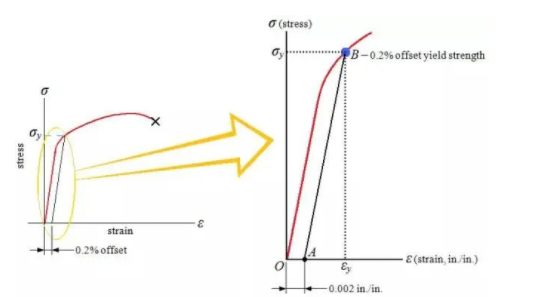
金屬の収率は転位の移動の結果であるため、金屬の収率は転位の移動抵抗によって決まります。純金屬の場合、格子抵抗、転位相互作用抵抗、および他の欠陥または構造との転位相互作用抵抗が含まれます。
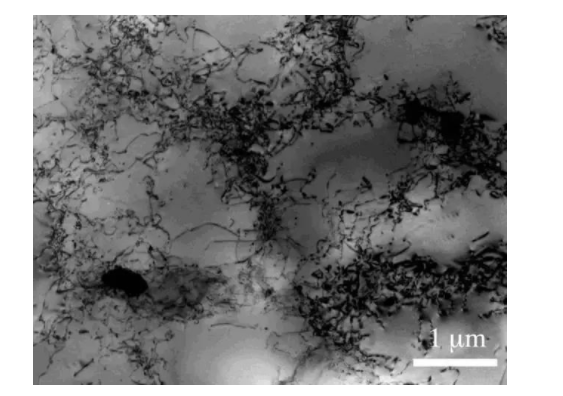
引張曲線の直線部分、つまり弾性部分に相當する部分が弾性特性です。弾性変形の開始から破壊の過程まで、サンプルが吸収する全エネルギーを破壊仕事と呼び、破壊前の金屬が吸収するエネルギーを破壊靭性と呼びます。通常、実際の金屬の機械的特性は引張プロセス中に変化します。最も顕著な現(xiàn)象は加工硬化です。金屬の加工硬化は、実際のエンジニアリング コンポーネントが過負荷時に突然破損し、悲慘な結果を招くことを回避するのに役立ちます。
金屬の塑性変形と変形硬化は、金屬の均一な塑性変形を確保するための前提條件です。つまり、多結晶金屬では塑性変形が起こると、それが強化され、その後、塑性変形が抑制されるため、変形が他の場所に伝わりやすくなります。
実際の引張曲線によると、ほとんどの金屬が室溫で降伏した後、降伏応力の作用下では変形が継続せず、変形を継続するには抵抗を増やす必要があります。真の応力-ひずみ曲線では、レオロジー応力が上昇し、加工硬化現(xiàn)象が現(xiàn)れます。このような曲線を加工硬化曲線と呼びます。加工硬化指數(shù) n は重要な塑性指數(shù)であり、材料が連続変形に抵抗する能力を表します。
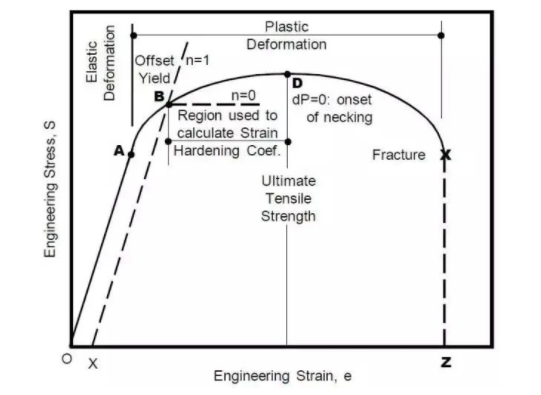
最後に、歪み率について話しましょう。一般に、金屬材料の引張曲線は、より低いひずみ速度で試験することによって得られます。高ひずみ速度下での機械的特性をテストする必要があるのは、一部の特別な金屬コンポーネント、つまり高速変形を伴うコンポーネントのみです。通常の室溫では、材料の変形は主に転位すべりまたは雙晶です。
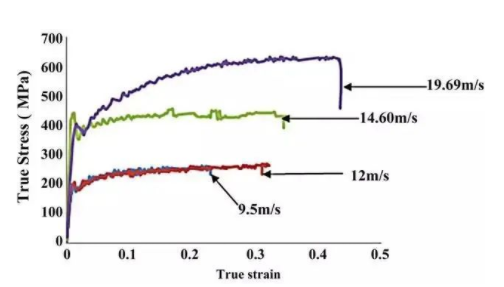
引張曲線上の最大工學応力、つまり工學ひずみ曲線は、極限引張応力、つまり引張強度と呼ばれます。