下の図に示すように、コーナー半徑は、交差線の主刃先と側(cè)面刃先によって形成されます。これは、エッジ半徑とも呼ばれます。
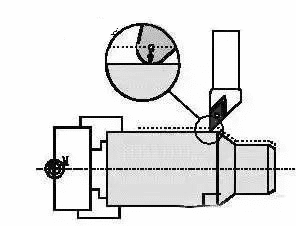
切削工程では、工具先端の強度を向上させ、機械の表面粗さを低減するために、通常、円弧遷移エッジが工具先端に存在します。その上、一般的な非再研磨ブレードは、特定の半徑の遷移として円弧を持っています。専ら鋭利なターニングチップですが、それでも一定のアーチ型の面取りを持っています。ターニングチップには絶対的なコーナーはありません。
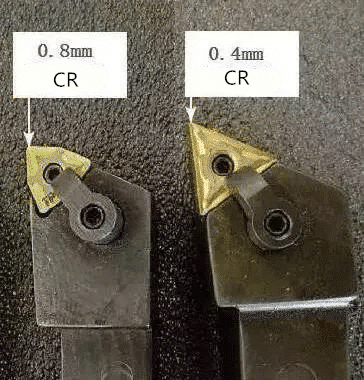
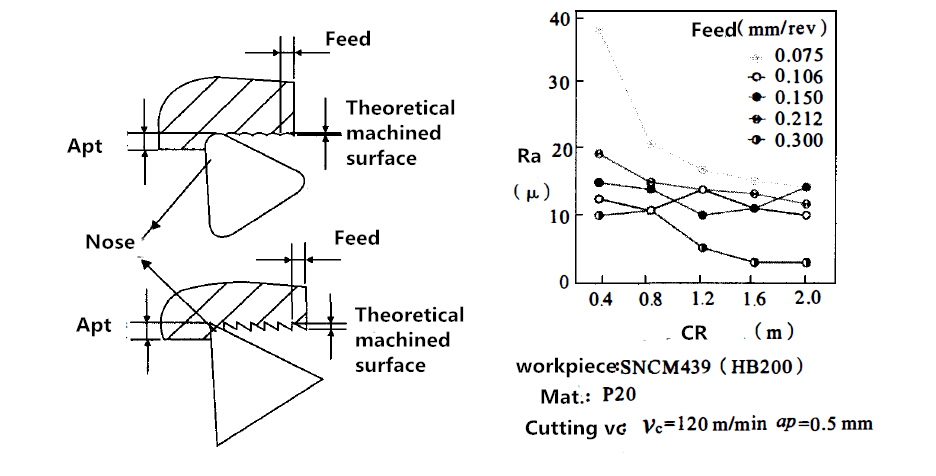
図1の比較から、工具ノーズ半徑と1回転あたりの送りがワークピースの表面粗さに最も大きな影響を與えることがわかります。理論的な表面粗さ要件を達成するには、正しい工具ノーズ半徑と送り速度を使用します。選択する必要があります。下の図は、これら3つの要素の値の関係の參照表です。一般に、工具先端のコーナー半徑は、送り速度の3?4倍に適しています。
f | Ra | |||||
r | 0.4 | 0.8 | 1.2 | 1.6 | 2.0 | |
1.6 | 0.07 | 0.1 | 0.12 | 0.14 | 0.16 | |
3.2 | 0.1 | 0.14 | 0.18 | 0.2 | 0.23 | |
6.3 | 0.14 | 0.2 | 0.25 | 0.28 | 0.32 | |
12.5 | 0.2 | 0.28 | 0.35 | 0.4 | 0.45 | |
25 | 0.28 | 0.4 | 0.49 | 0.56 | 0.63 |
rコーナー半徑mm
回転あたりのf最大送り。んん
Ra粗さμm
工具先端半徑の半徑と1回転あたりの送りを選択するために、理論的な実験式(1)によって決定することもできます。
Ra = f2/ r * 125
ここで:
Ra (μm) – 表面粗さ;
f(mm/rev) – 1 回転あたりの送り;
r (mm) – 工具先端円弧の半徑;
125 —定數(shù)。
工具先端半徑の半徑と送り量(1)の設(shè)定値を代入すると、理論的な表面粗さや表面粗さも計算できます。
例:工具先端円弧の半徑は0.8 mm、送り速度は
0.2 mm / r、理論的な表面粗さを式(1)に置き換えます。
Ra = 0.22/0.8*125=6.25μm
理論的な表面粗さは6.25μmです。
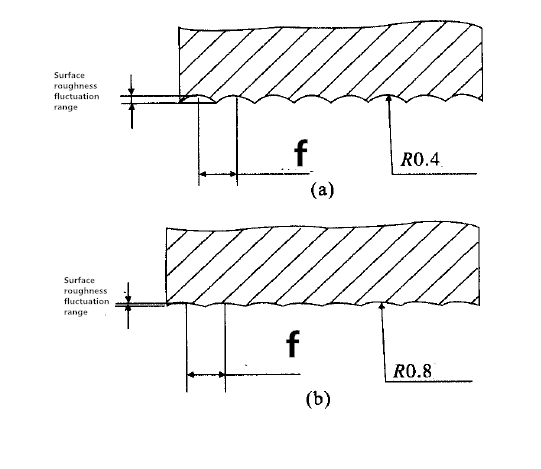
半徑が大きすぎると、工具とワークピースが過度に接觸して振動が発生することに注意してください。逆に、半徑が小さすぎると、先端が弱くなり、すぐに摩耗します。頻繁に再研磨する必要があるため、フィレット半徑は通常0.3?0.4mmです。
コナー半徑(エッジ半徑)補正
CNC旋盤を加工する場合、角半徑を補正する必要があります。
プログラミング時には、ツールチップは通常ポイントと見なされますが、実際には角が丸くなっています。軸に平行または垂直な端面、外徑、內(nèi)徑などの表面を、理論上の先端點に従ってプログラムされたプログラムで処理する場合、エラーは発生しません。
ただし、実際の処理では、オーバーカットやマルチカットが発生します。次の2つの狀況について説明します。
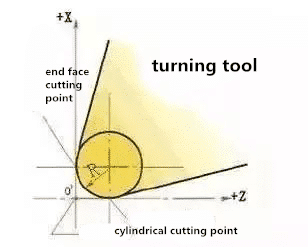
- 回転端面と內(nèi)外の円筒面
下の図は、円弧の先端とその向きを示しています。プログラミングと工具設(shè)定に使用される工具先端點は、理想的な工具先端點です。ツールノーズアークが存在するため、実際の切削點はツールエッジアークと切削面の接點です。端面を回転させるとき、工具先端円弧の実際の切削點は、理想的な工具先端點のZ座標と同じです。車の外穴と內(nèi)穴を使用する場合、実際の切削點と理想的な工具先端點のX座標値は同じです。したがって、端面と內(nèi)外円筒面を旋削する際に、刃先R補正を行う必要はありません。
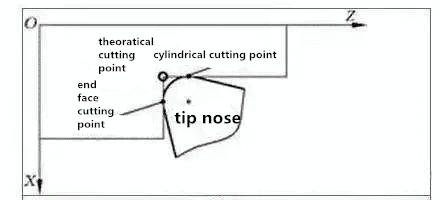
2)テーパー面とアーク面を加工する際にテーパー面とアーク面を回転させる
加工経路が機械軸と平行でない場合、実際の切削點と理想的な工具先端點との間にXおよびZ座標方向の位置偏差があります。下図に工具先端半徑が加工精度に與える影響を示します。理想的な工具先端でプログラムすると、カットやオーバーカットが少なくなり、加工エラーが発生します。工具先端円弧の半徑が大きいほど、加工誤差が大きくなります。
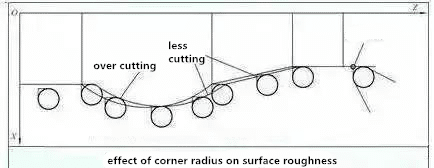
旋削工具の実際の加工では、プロセスやその他の要件により、工具の先端は理想的な點ではなく、円弧であることがよくあります。座標軸に平行な円筒および端面の輪郭を加工する場合、工具先端円弧はそのサイズと形狀に影響しませんが、円錐や円弧などの非座標方向の輪郭を加工する場合、工具の切削點は工具エッジ円弧になります。上向きに変化すると、工具先端の円弧によって寸法と形狀のエラーが発生し、カットが増減します。工具先端に起因するこの種の加工誤差は、理想的な點ではなく、円弧であり、工具の先端半徑補正機能によって除去できます。