In recent months, the mask market demand is massive, driving the mask related industry chain is also busy with production. Subscribers in the machining industry estimate that they have heard of three popular products produced by mask machines: printing rollers, melt blown die heads and ultrasonic fusion machines. Let’s talk about the meltblown die head first today.
Starting from the “heart” of the mask, the production of the melt blown cloth is inseparable from the melt blown die head. The uniformity and stability of the discharge of the melt blown die head play a decisive role in the quality of the melt blown cloth. So, how is the melt blown die head made?
How to produce melt blown fiber?
Here is a picture for us to understand the critical position of the melt blown cloth in the mask. The figure below shows the position and thickness of the melt blown cloth of N95 mask:

Fig. 1. Sectional view of N95 mask, taken by scanning electron microscope
From the video below, let’s see how the melt blown cloth is produced.
The production process of melt blown cloth can be divided into two types: horizontal type and vertical type. The simple figure is as follows:

Figure 2. Production process of melt blown cloth
The technological process of melt blown: polymer preparation → melt extrusion → metering pump → melt blown die head assembly → melt fine flow drawing → cooling → receiving device.
Among them, the role of the melt blown die is to change the polymer melt or solution in the viscous flow state into a fine flow with a specific cross-section through the micropore, and to form a filament through the solidification medium such as air or solidification bath.
Polypropylene PP special material enters the flow channel of the melt blown die head after plasticization, and then enters the spinneret after uniform distribution. High temperature, high speed and high pressure hot air jet forms the melt blown nonwovens, which is the most critical filter material in the middle layer of the mask.
In order to reach the medical level, the uniform discharge of the melt blown die head is required to be very high. Next, let’s learn more about how the melt blown die head is made.

For the manufacturing of melt blown die head, it is the key and difficult point to process the micro holes of spinneret.
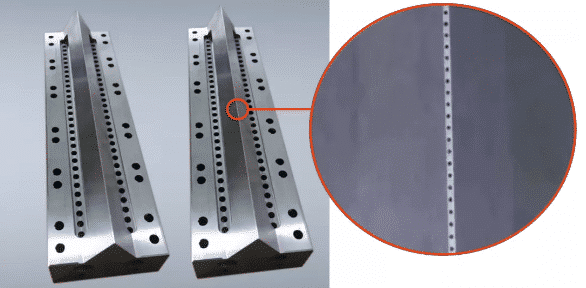
In the production of melt blown cloth, polypropylene (PP) is produced by flying out the spinneret micropores of melt blown die head, with the minimum diameter of micropores of 0.1-0.3mm. Most of the melt blown die heads are rectangular spinnerets, which are generally made of SUS316L, SUS304, sus630, sus431 and other stainless steel. The section shape is shown in the figure below.
The methods of processing micropores on hard materials include the use of piercer; the use of Mikron, Muye V33, Beijing Jingdiao, brother, Taiqun and other processing centers for micro drilling production; the use of Muye release motor production. Next, we will expand specifically:
Main processing methods
Machining center drilling
Spinneret micro hole is usually drilled by machining center, but the tool life is not stable because the hole is too small. Once the predicted cutter is broken ahead of time, even the whole spinneret will be scrapped when the bit cannot be taken out. Process a Φ 0.2mm spinneret micro hole, the processing time is about 30 seconds, and a good drill can drill more than 300 holes.

Advanced version: spindle machining
In the processing of spinneret micropores, drilling in machining center is a common method. However, there are some limitations in improving the production capacity. One is that the machining efficiency of the common spindle is not high, and the other is that the tool life fluctuation will lead to the cutting in advance, which will lead to the whole die scrapping due to the difficulty in getting the drill bit. The use of high-speed and high-precision motorized spindle will help to solve the above two problems.

Numerical control electric spark
It can solve the problem of drilling broken bit and burr at the bottom.
In order to solve this problem, some factories use copper infiltrated graphite electrode. Because the electrode is not easy to make, and the copper electrode is easy to produce burr and deformation.
Laser drilling technology
Some factories use laser to process spinneret micro holes. Laser drilling technology is to use high power density laser beam to irradiate the processed material, so that the material is heated to the vaporization temperature quickly, and the vaporization forms the hole. Its biggest advantage is high machining efficiency, only a few seconds to process a hole, but the corresponding processing equipment is very expensive.
Manufacturers of melt blown die head at home and abroad
The precision requirement of melt blown die head is very high, and it is very difficult to process. There are only a few enterprises in the world that can produce high-end melt blown die heads. The main suppliers are in Japan and Germany, such as Carson, Japan spinneret, enka, etc., and the processing time will take several months.
