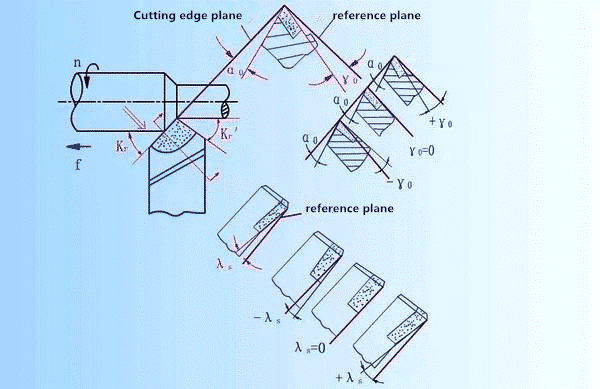
Quando si taglia il metallo, l'utensile taglia il pezzo e l'angolo dell'utensile è un parametro importante utilizzato per determinare la geometria della parte tagliente dell'utensile. Per comprendere in modo semplice l'angolo dell'utensile da taglio del tornio, iniziamo dagli angoli dell'utensile da taglio a punto singolo, che viene mostrato come segue,
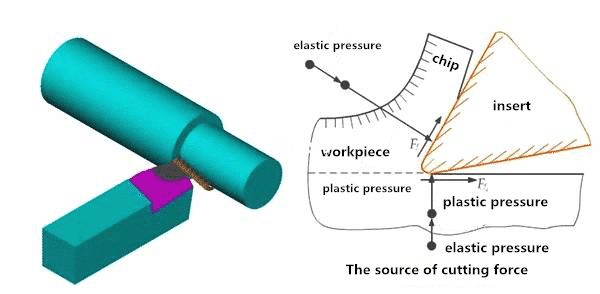
- La composizione della parte di taglio: 1 angolo, 2 bordi e 3 facce
La parte tagliente di un utensile è la faccia, il piano del fianco maggiore, il piano del fianco minore, il tagliente laterale, il tagliente finale e l'angolo.
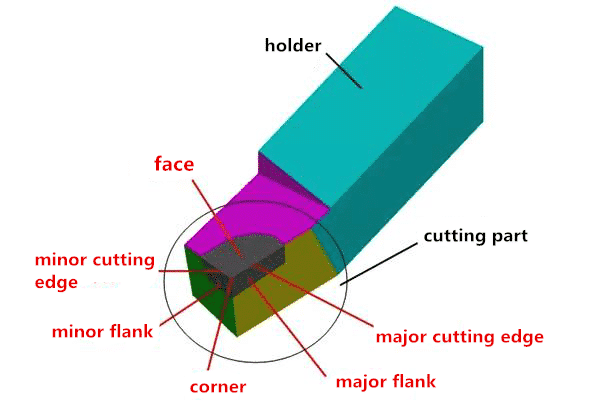
1)viso La superficie su cui scorrono i trucioli sull'utensile.
2)piano del fianco maggiore La superficie dell'utensile che si oppone e interagisce con la superficie lavorata sul pezzo, denominata piano del fianco maggiore.
3)piano del fianco minore La superficie dell'utensile che si oppone e interagisce con la superficie lavorata sul pezzo, denominata piano del fianco minore.
4)tagliente laterale L'intersezione tra la faccia dell'utensile e il piano del fianco maggiore è chiamata tagliente laterale.
5)tagliente finale L'intersezione della faccia dell'utensile con il piano del fianco minore è chiamata tagliente finale.
6)angolo L'intersezione del tagliente laterale e del tagliente finale è chiamata angolo. L'angolo è in realtà una piccola curva o linea retta, chiamata angolo arrotondato e angolo smussato.
2. Piano ausiliario per la misurazione dell'angolo di taglio dell'utensile di tornitura
Per determinare e misurare la geometria dell'utensile di tornitura, vengono selezionati tre piani ausiliari come riferimento. I tre piani ausiliari sono il piano del tagliente, il piano di riferimento (Base) e il piano ortogonale.
1)piano tagliente——Tagliare in un punto selezionato del tagliente laterale e perpendicolare al piano del piano inferiore del portautensile.
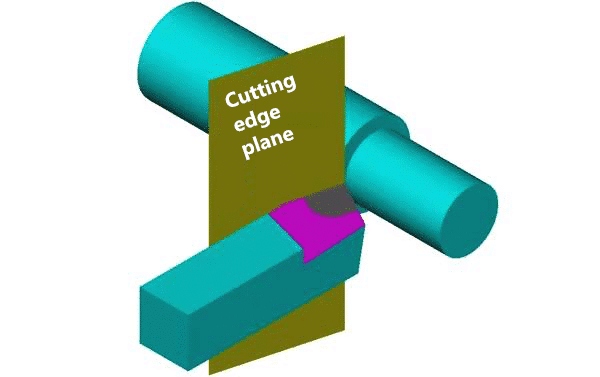
- piano di riferimento (base)——Passare un punto selezionato del tagliente laterale e parallelo al piano del fondo del portautensile.
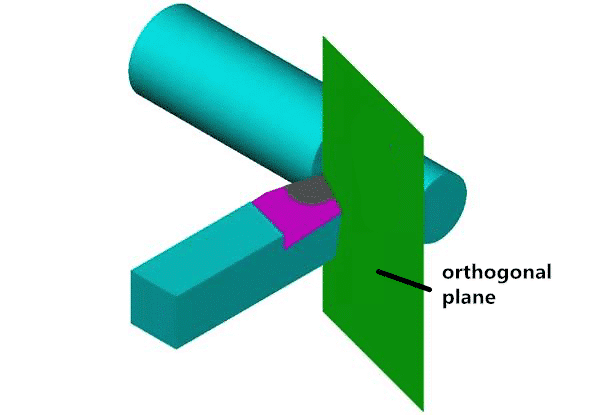
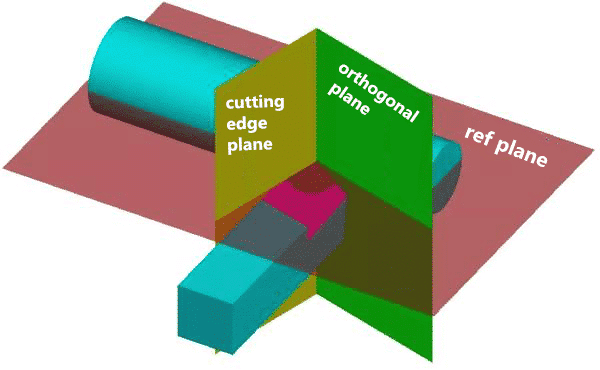
Si può vedere che i tre piani di coordinate sono perpendicolari tra loro per formare un sistema di coordinate rettangolari spaziali.
3.l'angolo geometrico principale e la scelta degli utensili di tornitura
1) principio di selezione dell'angolo di spoglia (γ0)
La dimensione dell'angolo di spoglia risolve principalmente la contraddizione tra la fermezza e l'affilatura della testa di taglio. Pertanto, l'angolo di spoglia deve essere innanzitutto selezionato in base alla durezza del materiale lavorato. La durezza del materiale lavorato è elevata e l'angolo di spoglia assume un valore piccolo e viceversa. In secondo luogo, la dimensione dell'angolo di spoglia deve essere considerata in base alle proprietà di lavorazione. L'angolo di spoglia deve essere considerato un valore piccolo durante la sgrossatura, mentre l'angolo di spoglia deve essere considerato un valore elevato durante la finitura. L'angolo di spoglia è generalmente selezionato tra -5° e 25°.
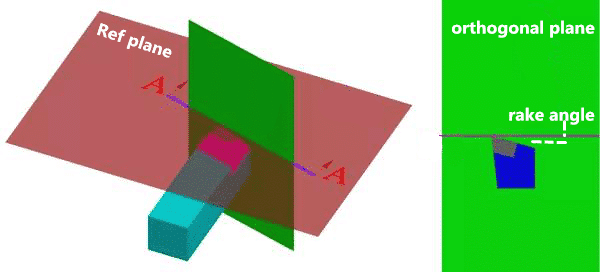
Di solito, l'angolo di spoglia (γ0) non è preimpostato al momento della realizzazione dell'utensile di tornitura, ma si ottiene affilando la scanalatura del truciolo sull'utensile di tornitura. Il flauto è anche chiamato rompitruciolo. La sua funzione è:
a.Rompere i trucioli senza impigliarli.
b.Controllare la direzione del deflusso dei trucioli per mantenere la precisione della superficie lavorata.
c.Ridurre la resistenza al taglio e prolungare la durata dell'utensile.
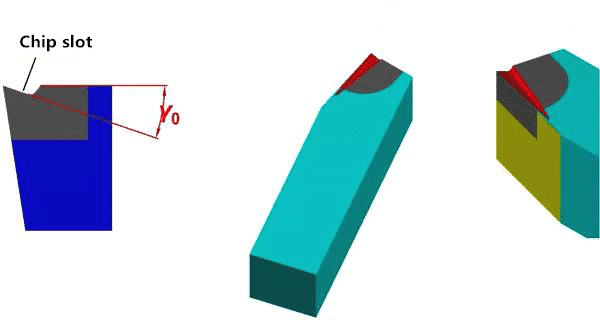
2)Principio di selezione dell'angolo di spoglia (α0)
Innanzitutto occorre considerare la natura del trattamento. Durante la finitura, l'angolo di spoglia assume un valore elevato, mentre durante la sgrossatura l'angolo di spoglia assume un valore piccolo. In secondo luogo, considerando la durezza del materiale lavorato, la durezza del materiale lavorato è elevata e l'angolo di spoglia principale viene portato a un valore basso per migliorare la fermezza della testa di taglio. In caso contrario, l'angolo di spoglia principale dovrebbe assumere un valore piccolo. L'angolo di spoglia non può essere zero o negativo ed è generalmente selezionato tra 6° e 12°.
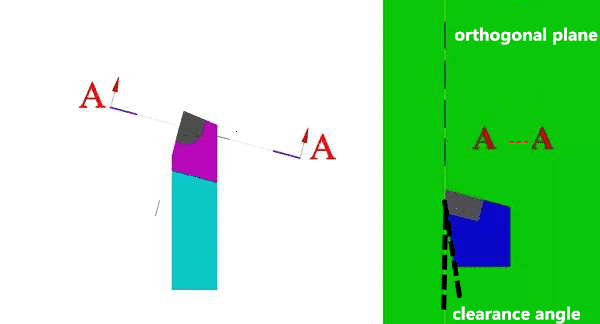
- principio di selezione dell'angolo del tagliente (Kr)
Innanzitutto occorre considerare la rigidità del sistema di lavorazione della tornitura costituito da torni, morse e utensili. Se il sistema è rigido, l'angolo del tagliente dovrebbe essere piccolo, il che è vantaggioso per migliorare la durata dell'utensile di tornitura, migliorare le condizioni di dissipazione del calore e la rugosità superficiale. In secondo luogo è necessario considerare la geometria del pezzo lavorato. Durante la lavorazione del gradino l'angolo del tagliente dovrebbe essere di 90°. Il pezzo tagliato al centro viene tagliato e l'angolo del tagliente è generalmente di 60 °. L'angolo del tagliente è generalmente compreso tra 30° e 90°, ma i più comuni sono 45°, 75° e 90°.
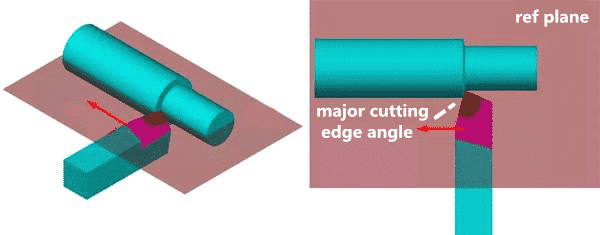
- Il principio della selezione angolo di taglio minore(Kr')
In primo luogo, l'utensile di tornitura, il pezzo in lavorazione e il morsetto hanno una rigidità sufficiente da essere presa in considerazione, in modo da ridurre l'angolo minore del tagliente. Altrimenti, si dovrebbe prendere il valore grande. In secondo luogo, considerando le proprietà di lavorazione, l'angolo minore del tagliente può essere preso come 10° in fase di rifinitura. 15°, durante la sgrossatura l'angolo minore del tagliente può essere di circa 5°.
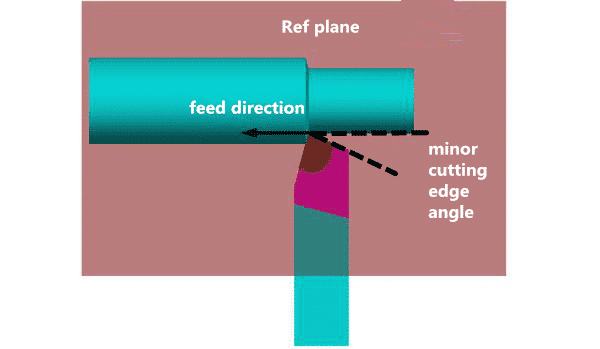
- Il principio della selezione inclinazione del tagliente(λS)
Dipende principalmente dalla natura del trattamento. Durante la sgrossatura, il pezzo ha un forte impatto sull'utensile di tornitura, assumendo λS ≤ 0°. Durante la finitura, il pezzo esercita una piccola forza di impatto sull'utensile di tornitura, considerando λS ≥ 0°. Di solito λS = 0°. L'inclinazione del tagliente è generalmente scelta tra -10° e 5°.
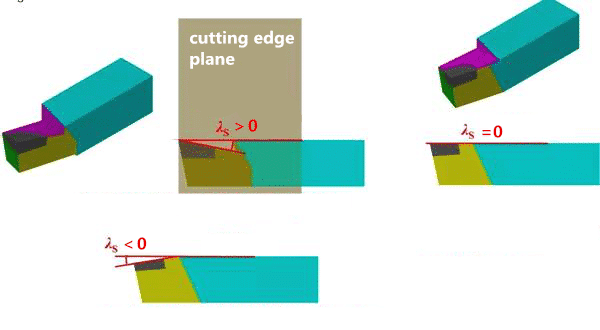