Quando durante la lavorazione vengono prodotti trucioli continui, non solo è facile graffiare la superficie del pezzo e danneggiare la lama, ma minacciano anche la sicurezza dell'operatore. Pertanto, è molto importante adottare le misure tecnologiche necessarie per controllare il tipo di truciolo e la rottura del truciolo nell'industria della lavorazione meccanica.
Because swarfs are the product of swarf layer deformation, changing cutting conditions is an effective way to change the types of swarfs and achieve swarf breaking. The factors affecting swarf processing conditions mainly include workpiece materials, tool geometry angle and swarf consumption.
General swarfs need to satisfy the following basic conditions:
1. swarfs shall not be entangled on cutting tools, workpieces and their adjacent tools and equipment.
2. swarfs should not splash to ensure the safety of operators and observers.
3. When finishing, swarfs can not scratch the machined surface of the workpiece, which affects the quality of the machined surface.
4. Guarantee the preset durability of the cutter, and do not wear out prematurely and try to prevent its damage.
5. When the swarf flows out, it does not interfere with the injection of cutting fluid; the swarf will not scratch the machine guide or other parts.
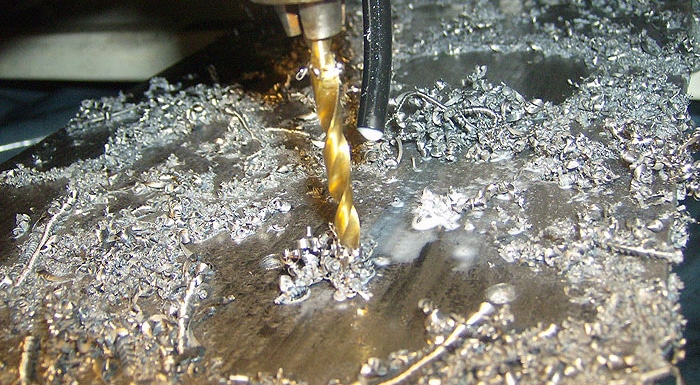
Classification of Swarf Shapes
Due to the different degree of plastic deformation, different kinds of swarfs may be produced, as shown in Figure 1. When processing plastic materials, band swarfs, nodal swarfs or granular swarfs are mainly formed. When processing brittle materials, fragmentary swarfs are generally formed.
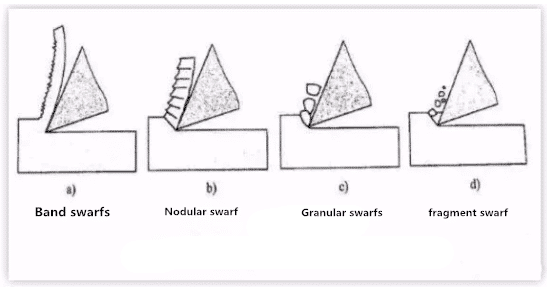
1. Band swarfs: Band swarfs are continuous, smooth bottom and fluffy back, as shown in Fig. 1-1a. Such swarfs are easily produced when plastic metal materials are machined with larger rake angle cutters at higher cutting speed. It is the product of insufficient deformation of cutting layer. When strip swarfs are produced, the cutting process is smooth and the surface roughness of the workpiece is small, but the swarfs are not easy to break, which often causes winding, roughening of the workpiece and even affects the operation, so the swarf breaking problem can not be ignored.
2.Nodular swarf: Nodular swarf is a kind of swarf with smooth bottom, obvious cracks on the back and deep cracks, as shown in Fig. 1-1b. Such swarfs are easily produced when plastic materials are machined at a lower cutting speed with a tool with reduced rake angle. It is the product of sufficient deformation of the swarf layer and has reached the degree of shear. When nodular swarfs are produced, the swarfs work unsteadily and the surface roughness of the workpiece is relatively large.
3. Granular swarfs: Granular swarfs are uniform granular swarfs, as shown in Fig. 1-1c. When using small rake angle tool to process plastic metal materials at very low cutting speed, it is easy to produce such swarfs. It is the product of fully deformed cutting layer, which achieves the shear failure of material and makes swarfs break along the thickness. When granular swarfs are produced, the cutting work is not stable and the surface roughness of the workpiece is relatively large.
4.fragment swarfs: fragment swarfs are irregular fine-grained swarfs, as shown in Fig. 1-1d. When cutting brittle materials, the swarf formed by the sudden cracking of the cutting layer after elastic deformation hardly passes through the plastic deformation stage. When crushing swarfs are formed, the cutting work is unstable, the blade is subjected to greater impact force, and the machined surface is rough and uneven.
It can be seen from the above that the types of swarfs vary with the workpiece materials and cutting conditions. Therefore, in the process of processing, we can judge whether the swarf condition is suitable or not by observing the swarf shape. We can also change the swarf shape by transforming the cutting condition, so that it can be transformed to the direction beneficial to production.
Principle of swarf breaking
In metal cutting process, whether swarfs are easy to break is directly related to the swarf deformation. Therefore, the study of swarf breaking principle must start with the study of the swarf deformation law.
swarfs formed in the cutting process will have higher hardness and lower plasticity and toughness due to relatively large plastic deformation. This phenomenon is called cold hardening. After cold hardening, swarfs become hard and brittle, and are easy to break when subjected to alternating bending or impact loads. The larger the plastic deformation the swarf undergoes, the more obvious the hardness and brittleness phenomena are, and the easier it is to break. When cutting materials with high strength, high plasticity and high toughness which are difficult to break swarfs, we should try to increase the deformation of swarfs in order to reduce their plasticity and toughness, so as to achieve the purpose of swarf breaking.
swarf deformation can be divided into two parts:
The first part is formed in the cutting process, which we call basic deformation. The swarf deformation measured by free cutting with flat rake face turning tool is close to the value of basic deformation. The main factors affecting the basic deformation are tool rake angle, negative chamfering and cutting speed. The smaller the front angle, the wider the negative chamfer and the lower the cutting speed, the larger the swarf deformation and the better the swarf breaking. Therefore, reducing the front angle, widening the negative chamfer and reducing the cutting speed can be used as measures to promote swarf breaking.
The second part is the deformation of swarfs in the process of flow and curling, which we call additional deformation. Because in most cases, only the basic deformation in the cutting process can not make swarfs break, it is necessary to add another additional deformation in order to achieve the purpose of hardening and breaking. The simplest way to force swarfs to undergo additional deformation is to grind (or press) a certain shape of swarf breaking groove on the rake face to force swarfs to curl and deform when flowing into the swarf breaking groove. swarfs are further hardened and embrittled after additional re-crimping deformation, and are easily broken when they collide with the workpiece or the flank.
Swarf breaking methodS
The fundamental reason for swarf breakage and continuity lies in the deformation and stress during swarf formation. When the swarf is in an unstable deformation state or the swarf stress reaches its strength limit, the swarf will break. Usually, the swarf will break after curling.
Reasonable selection of tool geometry angle, cutting parameters and swarf breaking groove are commonly used swarf breaking methods.
1. Reducing the rake angle and increasing the principal deviation angle: the rake angle and the principal deviation angle are the geometric angles of the tool which have great influence on swarf breaking. Reduce the front corner, increase swarf deformation, easy swarf breaking. Because small rake angle grinding will increase cutting force and limit the improvement of cutting parameters, tool will be damaged or even “stuffy” when it is serious. Generally, swarf breaking is not only done by reducing rake angle. Increasing the main deviation angle can increase the cutting thickness and easy swarf breaking. For example, under the same conditions, 90 degree knife is easier to break swarfs than 45 degree knife. In addition, increasing the main deflection angle is beneficial to reduce the vibration in processing. Therefore, increasing the main deflection angle is an effective swarf breaking method.
2.Reducing cutting speed, increasing feed and changing cutting parameters are another measures for swarf breaking. Increasing the cutting speed will make the bottom metal of the swarf soft and the swarf deformation insufficient, which is not conducive to swarf breaking; reducing the cutting speed will lead to swarf breaking. Therefore, in turning, swarfs can be broken by reducing the spindle speed and cutting speed. Increasing feed can increase cutting thickness and easy swarf breaking. This is a common swarf breaking method in processing, but it should be noted that with the increase of feed, the surface roughness of the workpiece will increase significantly.
3. Open swarf breaking groove: swarf breaking groove refers to the groove made on the rake face of the tool. The shape, width and oblique angle of swarf breaking groove are all factors affecting swarf breaking.
1) Shape of swarf breaking groove
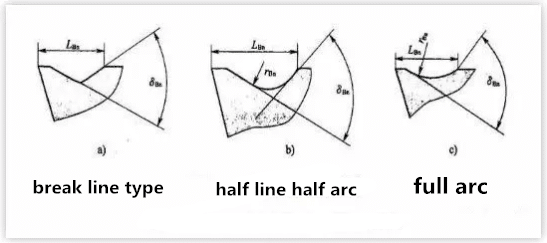
The commonly used swarf breaking grooves are three grooves, i. e. folded line, straight line and circular arc, and full circle arc, as shown in Figure 2.
When cutting carbon steel, alloy steel and tool steel, folded line, straight line arc and swarf breaking groove can be selected; when cutting high plastic material workpiece, such as pure copper, stainless steel workpiece, full circle arc swarf breaking groove can be selected.
2) Width of swarf breaking groove
The width of swarf breaking groove has a great influence on swarf breaking. Generally speaking, the smaller the groove width is, the smaller the curling radius of the swarf is, the greater the bending stress on the swarf is, and the easier it is to break. Therefore, smaller swarf breaking groove width is beneficial to swarf breaking. But the width of swarf breaking groove must be considered in connection with the cutting depth_p of feed.
C-shaped swarfs can be formed if the width of swarf breaking groove and feed rate are basically appropriate. If the swarf coiling groove is too narrow, it is easy to cause swarf blocking, which increases the load of turning tool and even damages the cutting edge; if the swarf coiling groove is too wide and the cutting curling radius is too large, the cutting deformation is not enough, and it is not easy to break, and often does not flow through the bottom of the groove to form continuous strip swarfs.
The width of the swarf groove should also be appropriate to the cutting depth. Otherwise, when the groove is too narrow, it will appear that the swarf width is not easy to curl in the groove, and the swarf will not flow through the bottom of the groove to form banded swarfs. When the groove is too wide, the swarf becomes narrow, the flow is more free, the deformation is insufficient, and it does not break.
In order to obtain satisfactory swarf breaking effect, the appropriate width of swarf breaking groove should be selected according to the specific processing conditions. For materials with lower hardness, slots should be narrower, whereas slots should be wider.