Today we continue to share some information about tungsten carbide dies by going back to the basics. The following cemented carbide dies are widely used in various industries, from nuts and bolts to grooves and missiles. Tungsten carbide molds and tools have become an important part of modern manufacturing industry. Metal and other hard materials are made into various shapes, parts and products by using the strength of tungsten carbide!
cold forming CARBIDE DIES
In cold forming, or cold heading, a cold metal slug will be put into the die, and then formed into the desired shape with a heavy blow. The impact force causes the metal to flow into the desired shape in the cemented carbide die by exceeding the yield strength of the metal. Modern cold forming is usually used for rapid forming metal parts such as screws, bolts and many other fasteners.
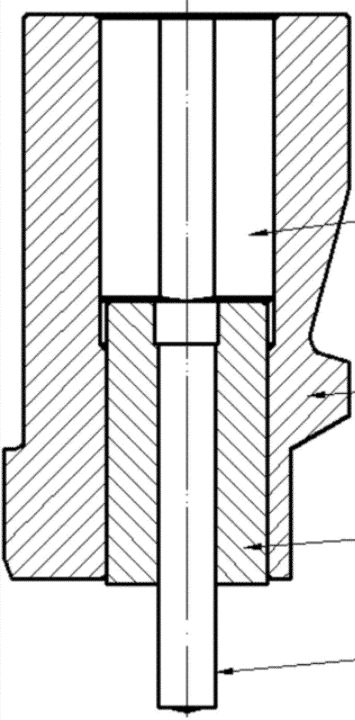
Cold heading materials can be copper, aluminum, carbon steel, alloy steel, stainless steel and titanium alloy, and the material utilization rate can reach 80 ~ 90%. Cold heading is mostly carried out on a special cold heading machine. The cold upsetting machine can complete the processes of material cutting, upsetting, accumulation, forming, chamfering, thread rolling, diameter reduction and edge cutting in sequence. The bar is automatically fed into a certain length by the feeding mechanism, and then cut into blank by the cutting mechanism. Finally, it is sent to the accumulation forming and punching station for cold upsetting by the clamp transmission mechanism.
??????? ???????? Drawing Dies
Wire drawing (wire drawing die) dies are usually used to form wire, bar, bar and pipe. Common drawing materials include steel, aluminum and copper.
what is drawing?
Drawing is a metal processing process, which uses tension to stretch (elongate) metal, glass or plastic. When a metal is drawn (pulled), it stretches and thins to obtain the desired shape and thickness. Drawing is divided into two types: sheet metal drawing and wire, bar and pipe drawing. Sheet metal drawing is defined as plastic deformation on the bending axis. For wire, bar and pipe drawing, the starting material is drawn through the die to reduce its diameter and increase its length. Drawing is usually carried out at room temperature, so it is classified as cold working process; However, large wires, bars or hollow sections can also be drawn at high temperatures to reduce the force.
why is tungsten carbide suitable for drawing metal?
Tungsten carbide has high compressive strength and can withstand extreme pressure; This material is ideal for deep drawing dies. Most major manufacturers use cemented carbide dies in the drawing process. Drawing materials include low carbon steel, stainless steel, high carbon steel and other steel alloys. Softer materials, such as aluminum or brass, are also often drawn.
The wire drawing process includes drawing through a die to reduce the diameter of the steel wire to the required size while keeping the volume unchanged. Draw the wire through a series of drawing dies to determine the size of the wire. The inner diameter of each die is slightly smaller than that of the previous die, so as to gradually reduce the width of the wire. The last mold in the series forms the wire to its target size.
Pipe drawing dies are usually round, hexagonal or square, but can be made into any shape required by the manufacturer. The tube drawing process is similar to the wire drawing process; However, the mandrel is used to form the internal dimensions of the tube. The mandrel is located in the tube and in the die. When the tube is pulled through the die, the mandrel will be formed inside to determine the wall thickness and inner diameter. A properly formed mandrel will form a smooth surface inside the pipe.
Bars and rods are drawn in a similar way to wire, but they tend to be much thicker. A variety of metals are used in this application, including many steels and copper alloys. The cutter is used to determine the size of the rod and the rod according to the length.
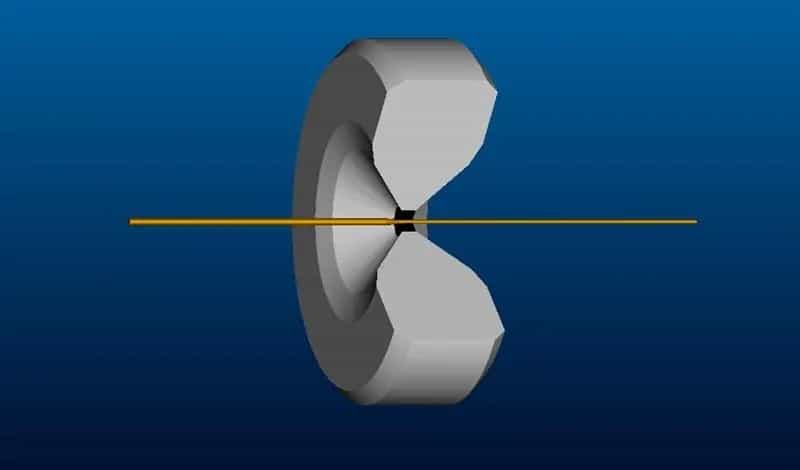
Carbide Extrusion Dies
Extrusion dies are usually used in a process in which slugs are pushed through the die to form the required cross-sectional area. If applied to pipes, use man drel in this process. Extrusion can be carried out in a variety of materials and at different temperatures to obtain the required properties of extruded products. Materials that can be formed with extrusion dies include steel, copper, aluminum, tin, lead, nickel, and even plastics. Products formed by extrusion include pipe, wire, bar, bar, pipe and electrode.
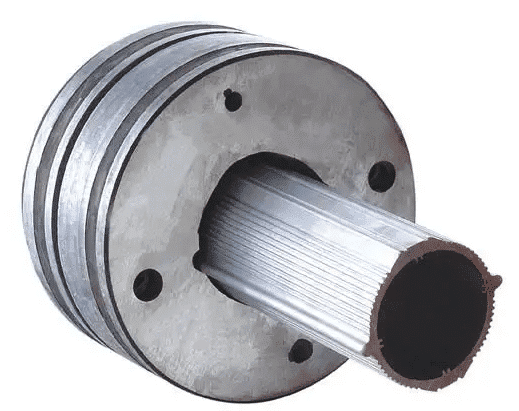
Common carbide die gradesYG15
????? | ????? (?? / ????2) | ?????? (?????) | ?????? (?????) | ???? ?? ???? (??) |
YG3X | 15.1 | ≥1700 | ≥92 | 0.8 |
YG6 | 14.9 | ≥2150 | ≥90 | 2 |
YG6X | 14.9 | ≥2300 | ≥91.5 | 0.8 |
YG8 | 14.8 | ≥2800 | ≥89.8 | 2 |
YG15 | 14 | ≥3000 | ≥87.5 | 2 |