La déviation mécanique systématique de la machine-outil peut être enregistrée par le système, mais en raison de facteurs environnementaux tels que la température ou la charge mécanique, la déviation peut encore appara?tre ou augmenter dans le processus d'utilisation ultérieur. Dans ces cas, SINUMERIK peut proposer différentes fonctions de compensation. L'écart est compensé en utilisant la valeur mesurée obtenue par le codeur de position réel (tel qu'un réseau) ou un capteur supplémentaire (tel qu'un interféromètre laser, etc.), afin d'obtenir un meilleur effet d'usinage.
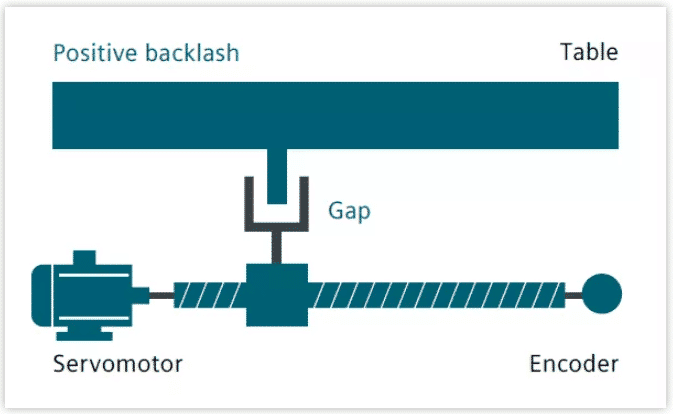
La transmission de force entre les pièces mobiles de la machine-outil et ses pièces motrices, telles que la vis à billes, produira une discontinuité ou un retard, car la structure mécanique sans jeu augmentera considérablement l'usure de la machine-outil, et il est également difficile réaliser en termes de technologie. Le jeu mécanique provoque un écart entre la trajectoire de déplacement de l'arbre / de la broche et la valeur mesurée du système de mesure indirect. Cela signifie qu'une fois que la direction change, l'axe se déplacera trop loin ou trop près, selon la taille de l'écart. La table de travail et son encodeur associé seront également affectés : si la position de l'encodeur est en avance sur la table de travail, il atteint la position de commande en avance, ce qui signifie que la distance de déplacement réelle de la machine-outil est raccourcie. Dans le fonctionnement de la machine-outil, en utilisant la fonction de compensation du jeu inverse sur l'axe correspondant, l'écart précédemment enregistré sera automatiquement activé lors de l'inversion, et l'écart précédemment enregistré sera superposé à la valeur de position réelle.
Compensation d'erreur de pas de vis
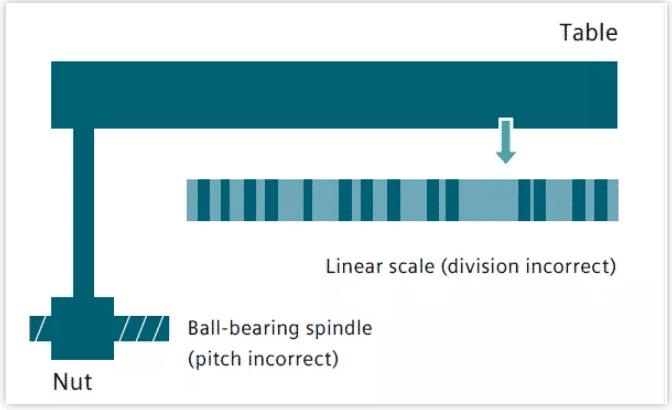
Le principe de mesure de la mesure indirecte dans le système de contr?le CNC est basé sur l'hypothèse que le pas de la vis à billes reste inchangé dans la course effective, donc en théorie, la position réelle de l'axe linéaire peut être déduite en fonction de la position des informations de mouvement du moteur d'entra?nement. Cependant, l'erreur de fabrication de la vis à billes entra?nera la déviation du système de mesure (également appelée erreur de pas de vis). L'écart de mesure (selon le système de mesure utilisé) et l'erreur d'installation du système de mesure sur la machine-outil (également appelée erreur du système de mesure) peuvent encore aggraver ce problème. Afin de compenser ces deux types d'erreurs, un ensemble de système de mesure indépendant (mesure laser) peut être utilisé pour mesurer la courbe d'erreur naturelle des machines-outils CNC, puis les valeurs de compensation requises sont enregistrées dans le système CNC pour compensation.
Compensation de frottement (compensation d'erreur de quadrant) et compensation de frottement dynamique
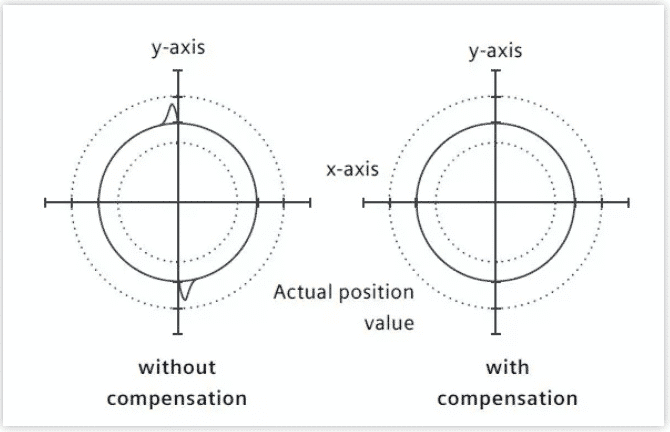
La compensation d'erreur de quadrant (également connue sous le nom de compensation de frottement) convient à toutes les situations ci-dessus, de manière à améliorer considérablement la précision du contour lors de l'usinage d'un contour circulaire. La raison est la suivante : dans la conversion quadrant, un axe se déplace à la vitesse d'alimentation la plus élevée et l'autre axe est immobile. Par conséquent, le comportement de frottement différent de deux axes peut entra?ner une erreur de contour. La compensation d'erreur de quadrant peut réduire efficacement cette erreur et assurer un excellent effet d'usinage. La densité de l'impulsion de compensation peut être réglée en fonction de la courbe caractéristique liée à l'accélération, qui peut être déterminée et paramétrée par un test de circularité. Dans le test d'arrondi, l'écart entre la position réelle du contour circulaire et le rayon programmé (notamment en marche arrière) est enregistré quantitativement, et affiché sur l'interface homme-machine par le biais de graphiques.
Dans la nouvelle version du logiciel système, la fonction de compensation de frottement dynamique intégrée peut compenser dynamiquement le comportement de frottement sous différentes vitesses de rotation de la machine-outil, réduire l'erreur de profil d'usinage réelle et obtenir une plus grande précision de contr?le.
Compensation d'erreur d'affaissement et d'angle
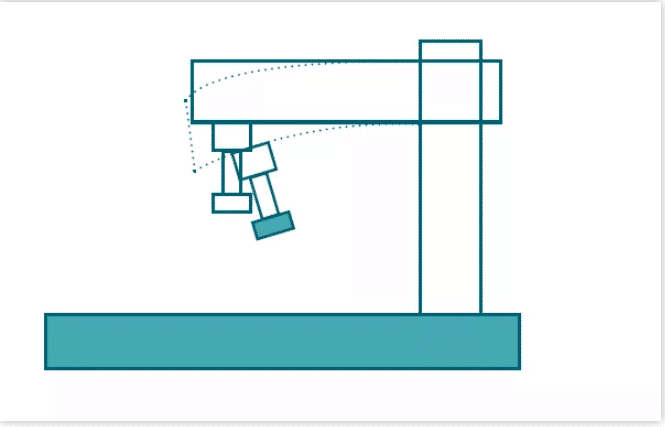
Si le poids des pièces individuelles de chaque machine-outil entra?ne un déplacement et une inclinaison des pièces mobiles, une compensation de l'affaissement est nécessaire car elle entra?nera l'affaissement des pièces concernées de la machine (y compris le système de guidage). La compensation d'erreur d'angle est utilisée lorsque les axes mobiles ne sont pas alignés les uns avec les autres à l'angle correct (par exemple, vertical). Avec l'augmentation du décalage de la position du point zéro, l'erreur de position augmente également. Ces deux erreurs sont causées par le poids de la machine-outil ou par le poids de l'outil et de la pièce. Une fois que la valeur de compensation mesurée est quantifiée lors du débogage, elle est enregistrée dans SINUMERIK en fonction de la position correspondante sous une forme, telle qu'un tableau de compensation. Lorsque la machine est en marche, la position de l'axe concerné est interpolée en fonction de la valeur de compensation du point de stockage. Pour chaque mouvement de trajectoire successif, il existe un axe de base et un axe de compensation.
compensation de température
La chaleur peut provoquer une dilatation de diverses parties de la machine. La plage de dilatation dépend de la température et de la conductivité thermique de chaque pièce de la machine. Une température différente peut entra?ner un changement de la position réelle de chaque axe, ce qui aura un impact négatif sur la précision de la pièce lors du traitement. Ces modifications des valeurs réelles peuvent être compensées par une compensation de température. Les courbes d'erreur de chaque axe à différentes températures peuvent être définies. Afin de compenser correctement la dilatation thermique à tout moment, la valeur de compensation de température, la position de référence et le paramètre d'angle de gradient linéaire doivent être transférés de l'automate au système de commande CNC via un bloc fonctionnel. Le changement de paramètres inattendus sera automatiquement éliminé par le système de contr?le, afin d'éviter de surcharger la machine et d'activer la fonction de surveillance.
Système de compensation d'erreur d'espace (VCS)
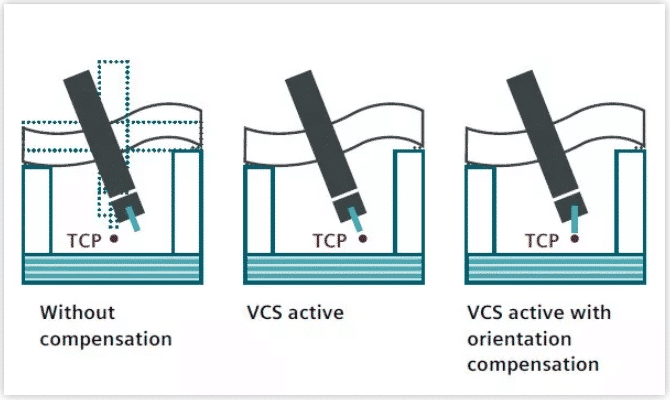
La position de l'arbre rotatif, leur compensation mutuelle et l'erreur d'orientation de l'outil peuvent entra?ner des erreurs géométriques systématiques de la tête rotative, de la tête rotative et d'autres composants. De plus, il y aura de petites erreurs dans le système de guidage de l'arbre d'alimentation de chaque machine-outil. Pour l'axe linéaire, ces erreurs sont des erreurs de position linéaire, des erreurs de rectitude horizontale et verticale, et pour l'axe de rotation, des erreurs d'angle de tangage, d'angle de lacet et d'angle de roulis seront générées. D'autres erreurs peuvent se produire lorsque les composants de la machine sont alignés les uns avec les autres. Par exemple, erreur verticale. Dans une machine-outil à trois axes, cela signifie que 21 erreurs géométriques peuvent se produire sur la pointe de l'outil : Six types d'erreurs par axe linéaire multipliés par trois axes, plus trois erreurs angulaires. Ces écarts forment ensemble l'erreur totale, également appelée erreur spatiale.
L'erreur d'espace décrit l'écart entre la position du point médian de l'outil (TCP) de la machine-outil réelle et celle de la machine-outil idéale sans erreur. Les partenaires de la solution SINUMERIK sont en mesure de déterminer les erreurs spatiales à l'aide d'équipements de mesure laser. Il ne suffit pas de mesurer uniquement l'erreur d'une seule position. Il est nécessaire de mesurer toutes les erreurs machine dans tout l'espace d'usinage. Généralement, il est nécessaire d'enregistrer les valeurs mesurées de toutes les positions et de tracer une courbe, car la taille de chaque erreur dépend de la position de l'axe d'alimentation concerné et de la position mesurée. Par exemple, lorsque l'axe Y et l'axe z sont dans des positions différentes, la déviation causée par l'axe x sera différente - même dans presque la même position de l'axe x. A l'aide du ? cycle996 – mesure de mouvement ?, il ne faut que quelques minutes pour déterminer l'erreur d'axe de rotation. Cela signifie que la précision de la machine-outil peut être constamment contr?lée et, si nécessaire, corrigée même en production.
Compensation d'écart (contr?le anticipatif dynamique)
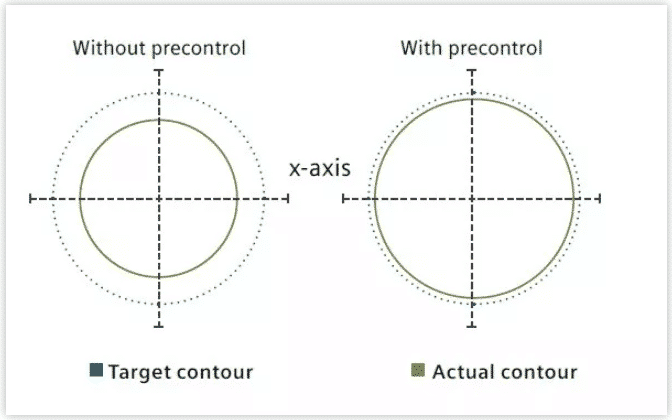
L'écart fait référence à l'écart entre le contr?leur de position et la norme lorsque l'axe de la machine-outil se déplace. L'écart d'axe est la différence entre la position cible de l'axe machine et sa position réelle. L'écart entra?ne des erreurs de contour inutiles liées à la vitesse, en particulier lorsque la courbure du contour change, comme un cercle, un contour carré, etc. Avec l'aide de la commande de langage de haut niveau CN ffwon dans le programme pièce, l'écart lié à la vitesse peut être réduit à zéro lors du déplacement le long du chemin. La commande d'avance est utilisée pour améliorer la précision de la trajectoire, afin d'obtenir un meilleur effet d'usinage.
Compensation électronique du contrepoids
Dans les cas extrêmes, la fonction de contrepoids électronique peut être activée afin d'éviter que l'arbre ne s'affaisse et n'endommage la machine, l'outil ou la pièce. Dans un arbre de charge sans contrepoids mécanique ou hydraulique, l'arbre vertical s'affaissera de manière inattendue une fois le frein relaché. Lorsque le contrepoids électronique est activé, il peut compenser l'affaissement inattendu de l'arbre. Une fois le frein relaché, la position de l'arbre de statisme est maintenue par un couple d'équilibrage constant.