Classification by diameter
① The common diameters of metric (mm) knives are: 0.5, 1, 1.5, 2, 2.5, 3, 4, 5, 6, 8, 10, 12, 16, 20, 25, 28, 30, 32, 35, 40, 50, 63
② The common diameters of inch knives are: 1 / 8, 1 / 4, 1 / 2, 3 / 16, 5 / 16, 3 / 8, 5 / 8, 3 / 4, 1, 1.5 and 2
Classification by material
(1) High speed tool steel tool is the most common tool, cheap, easy to buy, but easy to wear, wear and tear. Some Jinwei high speed tool steel tools with 3Co, Mn and other alloys have good wear resistance and high precision, such as LBK, YG and other types of tools, but the price is relatively expensive.
(2) Alloy tool
It is made of common alloy materials, high temperature resistance, wear resistance, high spindle speed, high processing efficiency and processing quality. It can process high hard materials (such as welded mould), so it is expensive. It is generally used in high precision and high quality processing occasions
(3) Discarded blade
This kind of cutter is made of alloy, which can be replaced, has good wear resistance and moderate price, so it is widely used in steel processing
The shape of the blade is square, diamond and round. The two corners of square and rhombic cutter grains need to be replaced after wear, while the ring surface of round cutter grains can be used. Therefore, it has good durability. The commonly used models are 25r5, 30r5, 32r5, 35r6, 16r0.8, 20r0.6, 25r0.8, 6R1, 8r0.5 and 10r0.5、
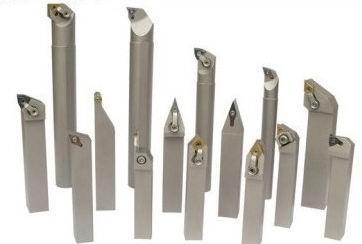
Classification by tool shape
Flat milling cutter
The surface milling cutter is generally divided into two parts
- Flat end milling cutter, rough milling, remove a large number of blanks, small area horizontal plane or contour finish milling;
- Ball end milling cutter, also called R cutter. Semi finish milling and finish milling of curved surface are carried out;
Application: widely used in various curved surface, arc groove processing. High temperature resistance: the maximum temperature for maintaining cutting performance is 450-550 / 500-600 ℃. - Flat end milling cutter with chamfer can be used for rough milling to remove a large number of blanks, and can also be used for fine milling of small chamfer on flat surface (relative to steep surface).
- Forming milling cutter, including chamfering cutter, T-shaped milling cutter or drum cutter, tooth cutter and inner r cutter.
- Chamfering cutter. The shape of chamfering cutter is the same as that of chamfering cutter, which is divided into milling round chamfering cutter and oblique chamfering cutter.
- T-shaped cutter can mill T-shaped groove;
- Gear cutter, milling out all kinds of gear, such as gear.
- Rough cutter, designed for aluminum copper alloy cutting, can be processed quickly
There are two common materials for flat milling cutter: high speed steel and cemented carbide. Compared with the former, the latter has high hardness and strong cutting force, which can improve the speed and feed rate, improve productivity, make the tool unobvious, and process stainless steel / titanium alloy and other difficult to machine materials, but the cost is higher, and it is easy to break the tool when the cutting force changes rapidly.
(1) T-shaped cutter: also known as T-shaped milling cutter, semicircle milling cutter and keyway milling cutter, it is used for processing row position groove
(2) Boring cutter: it is divided into rough boring cutter and fine boring cutter. Firstly, the bottom hole is pre processed with milling cutter or drill bit, and about 0.5 to 2 mm is reserved. Then the boring cutter is used for rough lining and fine lining processing. In this way, the precision of the round hole processed is relatively high, and the surface finish is also relatively high.
(3) Drill: used for round hole processing, the accuracy of the hole is not very good.
(4) Tap: for internal thread processing, may be used by hand, can also be installed on CNC machine tools.
(5) Reamer: a rotary cutter with one or more teeth for cutting off the thin layer of metal on the surface of a machined hole, and a rotary finishing cutter with straight or spiral edge for reaming or hole repairing.
(6) Ball flying knife: mainly on the alloy arbor, it is equipped with alloy ball cutter head. It is often used in semi finish machining and finish machining of curved surface with many dimensions.
(7) Center drill: used for positioning processing. For example, before drilling with drill bit, center drill is used for positioning.
(8) Lettering cutter: specially used for small font processing or pattern processing.
(9) Flat flying knife: the arbor is equipped with diamond shaped blades with small R radii at the opposite ends of the blades. It is often used for semi finishing and finishing curved surface (I have seen this kind of tool, but why is it called this name); extremely
It can be used for roughening if the side of the product or die is high, there is not much roughing allowance, and the tool diameter can cover the roughing allowance, but if it is used for die processing, the layer spacing is generally less than 0.3mm.
(10) Disk milling cutter: mainly used for rough machining of rough materials, large plane to material processing. - Flat end milling cutter, rough milling, remove a large number of blanks, small area horizontal plane or contour finish milling;
- Ball end milling cutter, also called R cutter. Semi finish milling and finish milling of curved surface are carried out;
Application: widely used in various curved surface, arc groove processing. High temperature resistance: the maximum temperature for maintaining cutting performance is 450-550 / 500-600 ℃. - Flat end milling cutter with chamfer can be used for rough milling to remove a large number of blanks, and can also be used for fine milling of small chamfer on flat surface (relative to steep surface).
- Forming milling cutter, including chamfering cutter, T-shaped milling cutter or drum cutter, tooth cutter and inner r cutter.
- Chamfering cutter. The shape of chamfering cutter is the same as that of chamfering cutter, which is divided into milling round chamfering cutter and oblique chamfering cutter.
- T-shaped cutter can mill T-shaped groove;
- Gear cutter, milling out all kinds of gear, such as gear.
- Rough cutter, designed for aluminum copper alloy cutting, can be processed quickly
There are two common materials for flat milling cutter: high speed steel and cemented carbide. Compared with the former, the latter has high hardness and strong cutting force, which can improve the speed and feed rate, improve productivity, make the tool unobvious, and process stainless steel / titanium alloy and other difficult to machine materials, but the cost is higher, and it is easy to break the tool when the cutting force changes rapidly.
(1) T-shaped cutter: also known as T-shaped milling cutter, semicircle milling cutter and keyway milling cutter, it is used for processing row position groove
(2) Boring cutter: it is divided into rough boring cutter and fine boring cutter. Firstly, the bottom hole is pre processed with milling cutter or drill bit, and about 0.5 to 2 mm is reserved. Then the boring cutter is used for rough lining and fine lining processing. In this way, the precision of the round hole processed is relatively high, and the surface finish is also relatively high.
(3) Drill: used for round hole processing, the accuracy of the hole is not very good.
(4) Tap: for internal thread processing, may be used by hand, can also be installed on CNC machine tools.
(5) Reamer: a rotary cutter with one or more teeth for cutting off the thin layer of metal on the surface of a machined hole, and a rotary finishing cutter with straight or spiral edge for reaming or hole repairing.
(6) Ball flying knife: mainly on the alloy arbor, it is equipped with alloy ball cutter head. It is often used in semi finish machining and finish machining of curved surface with many dimensions.
(7) Center drill: used for positioning processing. For example, before drilling with drill bit, center drill is used for positioning.
(8) Lettering cutter: specially used for small font processing or pattern processing.
(9) Flat flying knife: the arbor is equipped with diamond shaped blades with small R radii at the opposite ends of the blades. It is often used for semi finishing and finishing curved surface (I have seen this kind of tool, but why is it called this name); extremely
It can be used for roughening if the side of the product or die is high, there is not much roughing allowance, and the tool diameter can cover the roughing allowance, but if it is used for die processing, the layer spacing is generally less than 0.3mm.
(10) Disk milling cutter: mainly used for rough machining of rough materials, large plane to material processing.
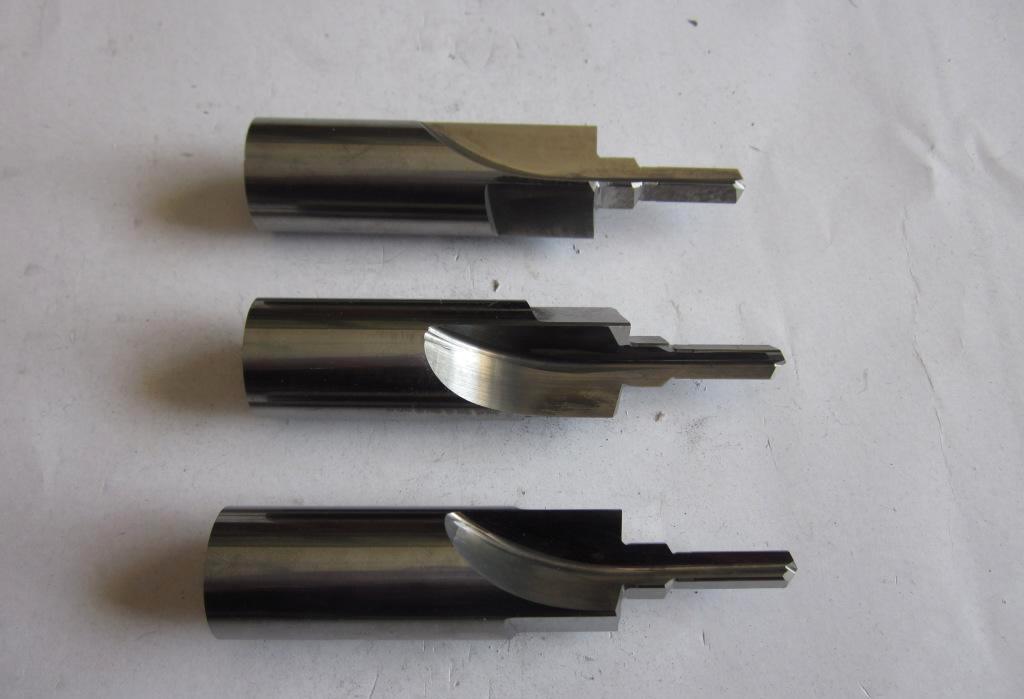
Selection of cutting tools
- Select tool according to processing material
① Steel material
Mild steel: such as 45 ° steel, 50 ° steel, imported trump steel, these materials are relatively easy to process, domestic high speed steel tool (such as ATA tool) can be processed, also can use imported YG, SKT, LBK tool processing
Hard steel: such as P20, 738, etc. these steel materials are made of domestic high-speed steel (such as ATA); they are difficult to process, so they can be processed with imported YG, SKT, LBK tools, or alloy tools.
Extra hard steel: such as S136, 718, oil steel, hardware alloy steel, etc. these materials are very hard, and can not be processed with domestic high-speed steel cutter (such as ATA cutter). At this time, alloy cutter can be used for processing.
② Copper and aluminum
These materials are relatively soft, generally can be processed with a variety of tools, but to consider the toughness of soft materials, so the tool to benefit, spindle speed is fast.
③ Quenched and welded mould materials shall be processed with alloy cutting tools. - Tool selection according to processing conditions
(1) Tool selection according to workpiece size
(2) The deeper the depth, the larger the tool diameter
(3) Choose the cutter according to the processing steps: rough machining should use big cutter, and generally use round nose cutter to roughen, ball cutter is strictly prohibited to roughen, while finish machining surface should use ball cutter, and the effect of finish machining surface with flat milling cutter or round nose cutter is not ideal (for example, according to finish machining, the cutter diameter is required)
Generally, the processing steps are as follows: using fire knife to roughen, small knife to roughen (clearing the residue left by fire knife), fire knife, light knife, small knife and light knife. Don’t add a whole workpiece with a knife to save trouble. The correct way of thinking is to use big knife to roughen the whole workpiece, and use small knife to process the remnant angle left by big knife. In order to avoid the empty knife and improve the processing efficiency, it is suggested to use regional processing to limit the cutting range
(4) Choose the cutter according to the processing efficiency: it is more efficient to use the flat milling cutter or round nose cutter to process the plane, while it is more efficient to use the slope cutter to process the smooth slope surface.
According to the size of the tool diameter, the most suitable tool length is selected.
Diameter 12 mm not exceeding 46 mm
Diameter 10 mm not exceeding 40 mm
Diameter 8 mm not exceeding 35 mm
Diameter 6 mm not exceeding 30 mm
Diameter 5 mm not exceeding 26 mm
Diameter 4 mm not exceeding 22 mm
Diameter 3 mm not exceeding 18 mm
Diameter 2 mm not exceeding 8 mm
Diameter 4 mm not exceeding 4 mm