1. Tool material
Die g?ngigen Werkzeugmaterialien beim Werkzeugschleifen sind: Schnellarbeitsstahl, pulvermetallurgischer Schnellarbeitsstahl, Hartmetall, PKD, CBN, Cermet und andere superharte Materialien. Werkzeuge aus Schnellarbeitsstahl sind scharf und z?h, w?hrend Hartmetallwerkzeuge eine hohe H?rte, aber eine geringe Z?higkeit aufweisen. Die Dichte des Hartmetallwerkzeugs ist offensichtlich h?her als die des Hochgeschwindigkeitsstahlwerkzeugs. Diese beiden Materialien sind die Hauptmaterialien für Bohrer, Fr?ser, Fr?ser und Gewindebohrer. Die Eigenschaften von PM-Schnellarbeitsstahl liegen zwischen den beiden oben genannten Materialien und werden haupts?chlich zur Herstellung von Schruppfr?sern und Gewindebohrern verwendet.
High speed steel tool is not sensitive to collision because of its good toughness. However, cemented carbide tool has high hardness and brittleness, and is sensitive to collision, and the edge is easy to jump. Therefore, in the process of grinding, the operation and placement of cemented carbide tools must be very careful to prevent the collision between the cutting tools or the falling of the cutting tools.
Because the accuracy of high-speed steel tools is relatively low, the grinding requirements are not high, and the price is not high, so many manufacturers set up their own tool workshops to repair and grind them. But cemented carbide tools often need to be sent to a professional grinding center for grinding. According to the statistics of some domestic tool grinding centers, more than 80% of the tools sent for repair are cemented carbide tools.
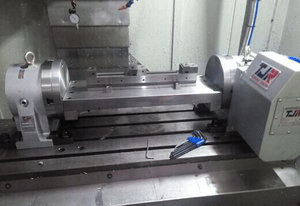
2. Tool grinder
Because the tool material is very hard, it can only be changed by grinding. In the manufacturing and grinding of cutting tools, the common tool grinders are as follows:
1) Groove grinding machine: grinding the groove or back of cutting tools such as drill bit and end mill.
2) Angle grinding machine: grinding the conical top angle (or eccentric back angle) of the drill bit.
3) Trimming machine: correct the transverse edge of the drill.
4) Manual universal tool grinder: grinding outer circle, groove, back, top angle, transverse edge, plane, rake face, etc. It is often used for tools with small quantity and complex shape.
5) CNC grinder: generally five axis linkage, the function is determined by software. It is generally used for grinding tools with large quantity and high precision, but not complicated, such as drill, end mill, reamer, etc. The main suppliers of these grinders are from Germany, Switzerland, the United States, Australia and Japan.

3. Grinding wheel
1) Abrasive
The grinding grains of different materials are suitable for grinding different kinds of cutting tools. In order to ensure the best combination of edge protection and machining efficiency, the wear particle size required for different parts of the tool is also different.
Alumina: used for grinding HSS tools. The grinding wheel is cheap and easy to be modified into different shapes for grinding complicated cutting tools (corundum).
Silicon carbide: used to modify CBN grinding wheel and diamond wheel.
CBN (cubic boron carbide): used for grinding HSS tools. High price, but durable. Internationally, grinding wheel is represented by B, such as b107, in which 107 is the size of abrasive particle diameter.
Diamond: used for grinding HM cutting tools, high price, but durable. The grinding wheel is represented by D, such as d64, where 64 represents the size of the abrasive particle diameter.
2) Shape
In order to facilitate the grinding of different parts of the cutter, the grinding wheel should have different shapes. The most commonly used are: parallel grinding wheel (1A1): grinding top angle, outer diameter, back, etc. Disc grinding wheel (12v9, 11v9): grinding spiral groove, milling cutter’s main and auxiliary cutting edge, trimming transverse edge, etc. After a period of use, the grinding wheel needs to modify its shape (including plane, angle and fillet R). In order to improve the grinding ability of the grinding wheel, the chip filling between the abrasive grains must be removed by using the cleaning stone frequently.
4. Grinding standards
Whether there is a set of good tool grinding standards is the standard to measure whether a grinding center is professional. In the grinding standard, the technical parameters of cutting edge of different cutting tools when cutting different materials are generally specified, including edge inclination angle, top angle, front angle, back angle, chamfering, etc. (in cemented carbide bits, the process of passivating the cutting edge is called “cutting edge”, and the width of the chamfered edge is related to the material to be cut, generally between 0.03 and 0.25 mm. The process of chamfering on the edge is called chamfering. Each professional company has its own grinding standards summarized for many years.
Difference between HM bit and HSS bit:
HSS bit: the top angle is generally 118 degrees, sometimes greater than 130 degrees; the blade is sharp; the requirements for accuracy (edge height difference, symmetry, circumferential runout) are relatively low. There are many ways to repair the horizontal blade.
HM bit: the top angle is generally 140 degrees; the straight slot drill is often 130 degrees, and the three edge drill is generally 150 degrees. The cutting edge and the edge (on the edge) are not sharp, and are often passivated, or called chamfering and chamfering. The transverse blade is often trimmed into S-shape to facilitate chip breaking.
Back angle: the back angle of the blade is very important to the tool. If the back angle is too large, the blade will jump easily and “stab the knife”; if the back angle is too small, the friction will be too large and the cutting will be unfavorable. The back angle of the tool varies with the material to be cut, the type of the tool and the diameter of the tool. Generally speaking, the rake angle decreases with the increase of tool diameter. In addition, if the material to be cut is hard, the back angle is smaller, otherwise, the rear angle is larger.
5. Tool detection equipment
Tool detection equipment is generally divided into three categories: tool setting instrument, projector and universal tool measuring instrument. The tool setting instrument is mainly used for tool setting preparation (such as length) of CNC equipment such as machining center, and also used to detect parameters such as angle, radius and step length; the function of projector is also used to detect parameters such as angle, radius and step length. However, the two methods mentioned above can not be used to measure the tool back angle. The universal tool measuring instrument can measure most of the geometric parameters of the tool, including the back angle.
Therefore, tool professional grinding center must be equipped with universal tool measuring instrument. But there are not many suppliers of this kind of equipment. There are German and French products on the market.
6. Grinding mechanic
The best equipment also needs to be operated by personnel and trained by grinding technicians