Mechanisms of Grain Growth Inhibition
The grain growth inhibitors primarily influence WC grain growth through the following approaches:
Solute Drag Effect
Principle:grain growth Inhibitor elements (e.g., V, Cr) dissolve into the WC or Co phase, adsorb at WC/Co phase boundaries or WC/WC grain boundaries, hindering atomic diffusion and grain boundary migration.
Elemental Solid Solution
Inhibitors such as VC and Cr?C? decompose during sintering, with V and Cr atoms dissolving into the WC lattice or Co binder phase.
Example: V substitutes W sites in WC (forming (V,W)C solid solution), while Cr dissolves into the Co phase (forming (Co,Cr) solid solution).
Grain Boundary Segregation
Solute atoms (e.g., V, Cr) enrich at WC grain boundaries or WC/Co interfaces, forming a “solute atmosphere.”
These segregated atoms pin grain boundaries, increasing the energy barrier for migration.
Drag on Grain Boundary Movement
When grain boundaries attempt to migrate, solute atoms must move along, but their slower diffusion rate impedes boundary motion.
Analogous to “viscous drag,” this suppresses WC grain coalescence and growth.
Applicable grain growth Inhibitors: VC, Cr?C? (primarily rely on solute drag).
Second-Phase Pinning Effect (Zener Pinning)
Principle: grain growth inhibitors form nanoscale carbide particles (e.g., (V,W)C, (Cr,W)C) that physically obstruct WC grain growth at boundaries.
Nanoparticle Precipitation
During sintering, decomposed VC or Cr?C? reprecipitate as nanoscale carbides (e.g., 5–50 nm (V,W)C particles), typically located at WC/WC or WC/Co interfaces.
Grain Boundary Pinning
Migrating boundaries must overcome the restraint of these nanoparticles, requiring additional energy.
According to the Zener equation, pinning force (F?) correlates with particle volume fraction (f) and size (r). Finer, denser particles yield stronger inhibition.
Suppression of WC Dissolution-Reprecipitation
Nanoparticles hinder WC dissolution in liquid Co and redeposition, reducing Ostwald ripening (“l(fā)arge grains consuming small ones”).
Applicable grain growth Inhibitors: VC (strongest pinning), Cr?C? (moderate), TaC/NbC (weaker).
Common Grain Growth Inhibitors and Their Characteristics
Mechanismus | Primary Inhibitors | Key Characteristics |
Solute Drag | VC, Cr?C? | Hinders grain boundary migration through solute atom segregation |
Second-Phase Pinning | VC, Cr?C? | Physically blocks grain boundaries via nanoparticle dispersion (Zener pinning) |
Dissolution-Reprecipitation Control | VC, Cr?C? | Reduces WC dissolution in Co binder and slows atomic diffusion |
Grain Boundary Energy Modification | TaC, NbC | Lowers grain boundary energy, enhancing high-temperature stability |
Selection and Optimization of grain growth Inhibitors
Ranking of Inhibition Effectiveness
VC > Cr?C? > TaC ≈ NbC
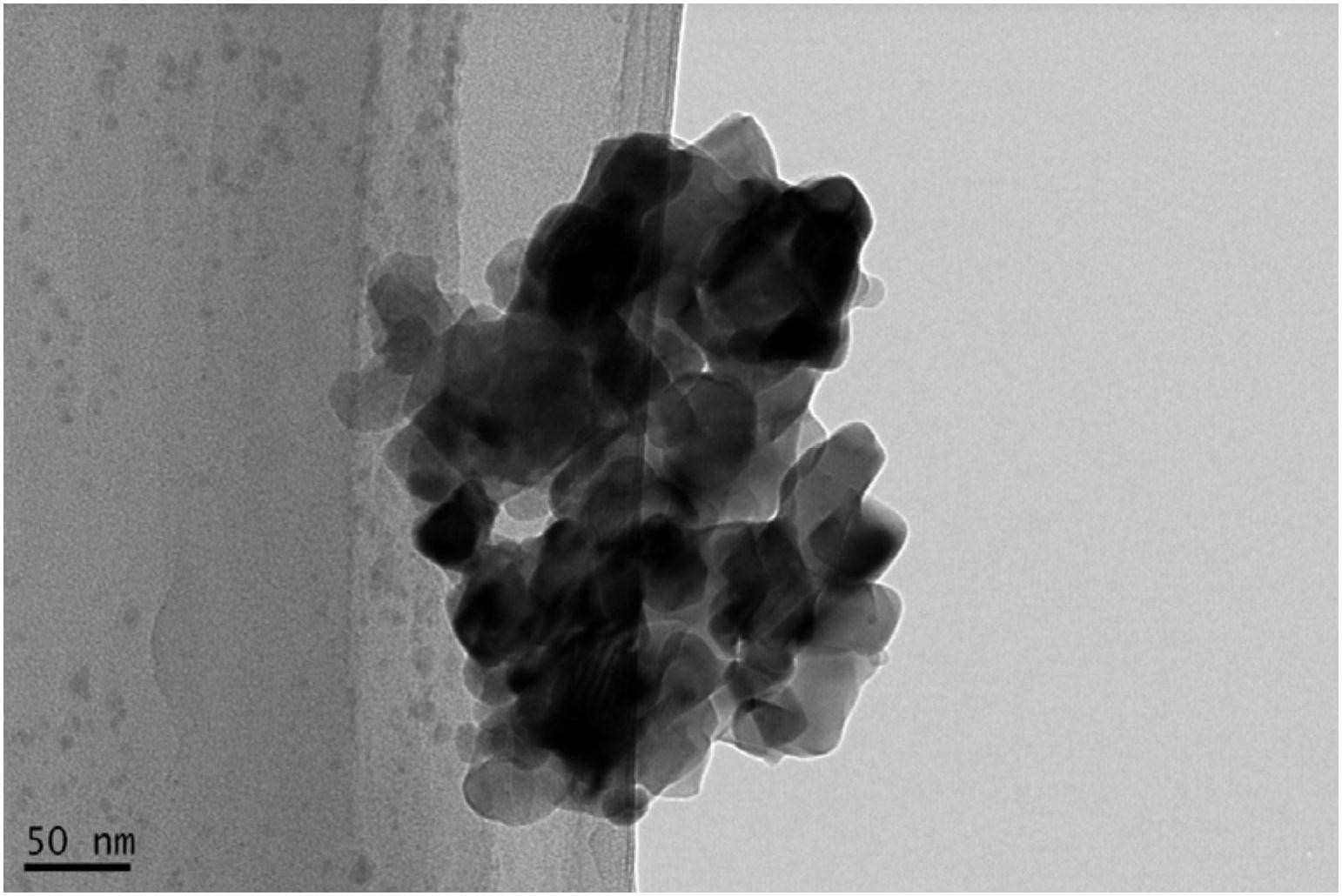
Key Influencing Factors
Sintering Temperature and Time:
High temperatures or prolonged sintering may weaken inhibitor effectiveness (e.g., VC particle coarsening).
Co Content
Alloys with higher Co require greater grain growth inhibitor content (due to enhanced WC dissolution in liquid Co).
Carbon Balance
Inhibitors may consume free carbon, necessitating carbon potential adjustment to avoid η-phase formation (e.g., Co?W?C).
Detailed Industrial Application Cases of Cemented Hartmetall Grain Growth Inhibitors
Grain growth inhibitors (e.g., VC, Cr?C?, TaC) are widely used in the cemented carbide industry, primarily in cutting tools, mining tools, and wear-resistant components. The selection of different inhibitors directly affects the alloy’s hardness, toughness, wear resistance, and high-temperature stability. Below is an in-depth analysis of several typical application cases.
Ultra-Fine Grain Cemented Carbide Cutting Tools (VC + Cr?C? Composite Inhibition)
Application Background
Requirement: High-speed cutting and precision machining (e.g., automotive engine blocks, aerospace titanium alloys) demand tools with both high hardness (>90 HRA) and chipping resistance.
Issue
Conventional WC-Co alloys have coarse grains (1–3 μm), exhibiting high hardness but low toughness, leading to edge chipping.
Solution
Ultra-fine grain cemented carbide (grain size 0.2–0.5 μm) achieved through VC (0.3–0.5 wt%) + Cr?C? (0.5–1.0 wt%) composite addition.
Inhibition Mechanism
VC: Nano-sized (V,W)C particles pin WC grain boundaries (Zener pinning), suppressing grain coalescence.
Cr?C?: Cr dissolves into the Co phase, reducing WC dissolution rate (solute drag) while enhancing oxidation resistance.
Representative Products
Sandvik GC4325: For titanium alloy machining, using VC+Cr?C? inhibition (0.3 μm grains).
Kennametal KCS10B: For stainless steel finishing, incorporating nano-VC.
Mining Cemented Carbide Drill Bits (TaC/NbC High-Temperature Inhibition)
Application Background
Requirement: Oil drill bits and tunnel boring machine cutters operate under high temperatures (>800°C) and impact loads, requiring thermal fatigue resistance and wear resistance.
Issue
Conventional WC-Co alloys experience rapid grain growth at high temperatures, reducing strength.
Solution
TaC (1–3 wt%) or NbC (1–2 wt%) addition to leverage their high-temperature stability for grain growth suppression.
Inhibition Mechanism
TaC/NbC: Form (Ta,W)C or (Nb,W)C solid solutions at high temperatures, pinning grain boundaries (Zener effect) and reducing boundary mobility.
Synergy with Co binder: Ta/Nb dissolution into Co increases liquid Co viscosity, slowing WC dissolution-reprecipitation.
Representative Products
Atlas Copco Button Bits: TaC-containing drill bits for granite drilling.
Sumitomo Electric DX Series: Oil drilling alloys with NbC for thermal stability.
Wear-Resistant Sealing Rings (Cr?C? Inhibition + Rare Earth Optimization)
Application Background
Requirement: Mechanical seals and bearing sleeves require high wear resistance + corrosion resistance (e.g., chemical pumps, seawater environments).
Issue
WC-Co suffers from selective corrosion of the Co phase in corrosive media, causing WC grain detachment.
Solution
Cr?C? (1.0–1.5 wt%) + rare earth oxides (Y?O? 0.1–0.3 wt%) composite addition.
Inhibition Mechanism:
Cr?C?: Forms (Cr,W)C particles to refine grains while improving corrosion resistance via Cr dissolution in Co.
Y?O?: Rare earth elements segregate at grain boundaries, purifying interfaces and strengthening boundary cohesion.
Representative Products
Mitsubishi Materials EX Series: Chemical pump seals with Cr?C? + rare earth modification.
Oerlikon Durit CR: Corrosion-resistant alloys with Cr?C?.
PCB Micro-Drills (Ultra-Fine VC + Sintering Process Optimization)
Application Background
Requirement: PCB micro-drills (diameter 0.1–0.3 mm) demand ultra-high precision (roundness <1 μm) and fatigue resistance.
Issue
Grain coarsening causes drill edge blunting and fracture during drilling.
Solution
Ultra-fine VC (0.2–0.4 wt%) + low-temperature sintering (1350°C, vs. conventional 1450°C).
Inhibition Mechanism
Nano-VC: Prepared via high-energy ball milling (<50 nm particles) for enhanced pinning.
Low-temperature sintering: Reduces Ostwald ripening time, preserving inhibitor efficacy.
Representative Products
Toshiba Tungaloy DLC-Coated Micro-Drills: Nano-VC inhibition technology.
TaeguTec PCB Drill: Optimized for high-layer PCBs.
Fazit
Grain growth inhibitors in cemented carbides control grain size through solute drag and second-phase pinning mechanisms. Their selection must be optimized based on material composition, sintering processes, and performance requirements. Future trends favor nano-composite inhibitors and multi-component synergistic regulation to further enhance comprehensive material properties.
Schreibe einen Kommentar
Deine E-Mail-Adresse wird nicht ver?ffentlicht.