Metal processing is inseparable from the blade. A good blade must have high wear resistance, long tool life, high metal removal rate and high reliability. It is even required to have high performance in dry cutting or wet cutting under severe conditions (such as complex cutting and deep cavity), so as to ensure small tolerance of workpiece size and excellent surface quality. Today, let’s see how the boss of the blade industry produces blades!
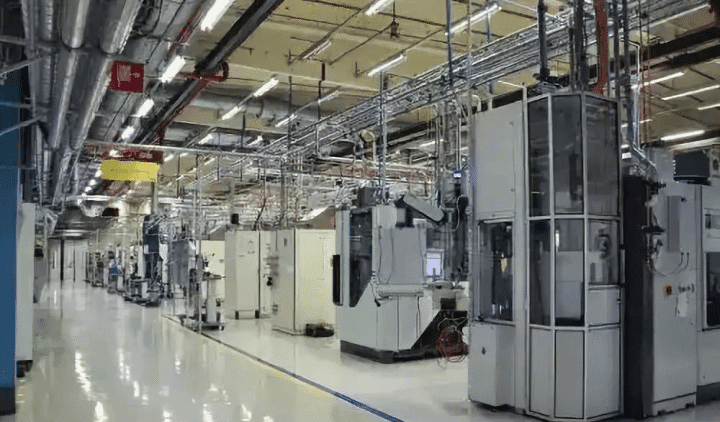
Insert matrix producing
The blade is made of 80% tungsten carbide and metal matrix. The function of metal matrix is to bond hard cemented carbide powder together, of which cobalt is the most common. The process of producing blades is very complex. It takes more than two days to complete, and there will be a lot of challenges. In addition to absolute precision and reliability, cleanliness is a prerequisite. The whole process must be well guaranteed without any carelessness.
The first step is to ensure that the composition ratio of each specific powder is just right. Tungsten is a limited raw material derived from Sandvik’s mine in Austria or recycled blade. Cobalt, titanium and all other components come from carefully selected suppliers who can ensure consistent quality without affecting the quality of finished products. Nevertheless, every batch must be meticulously tested in the laboratory for safety. The main components are then automatically distributed to containers at different stations along the weighing line. For some blades, a small amount of special ingredients need to be added manually. After passing through all the different stations, the full container will weigh hundreds of kilograms.
The next step is grinding, mixing the components in the container with ethanol, water and organic compounds, and grinding them to the required particle size: usually 0.1 ~ 5 microns in diameter. This process takes 8 ~ 55 hours, depending on the formula of the finished product. The compound is a gray slurry with a consistency similar to that of yogurt drinks. Then the slurry is pumped into the spray dryer, and the spray dryer evaporates the mixture of ethanol and water with hot nitrogen.
When the powder is dried, it consists of spherical particles with a diameter of about 100 microns. The samples were sent to the laboratory for quality inspection. Then, the ready-made powder is filled into a smaller barrel and processed by pressing machine, in which the organic compound acts as an adhesive, and the powder is bonded together after pressing. After the mold of a specific blade is in place, the inner cavity of the mold will be filled with powder. The machine tool can apply 50 tons of pressure when manufacturing a single blade. Even if the automation of the whole process is high, each blade will still be weighed, and then the operator will carry out appearance control at certain time intervals to ensure the highest quality and accuracy. At this stage, the blade is still very fragile, so the next step is to enter the sintering furnace.
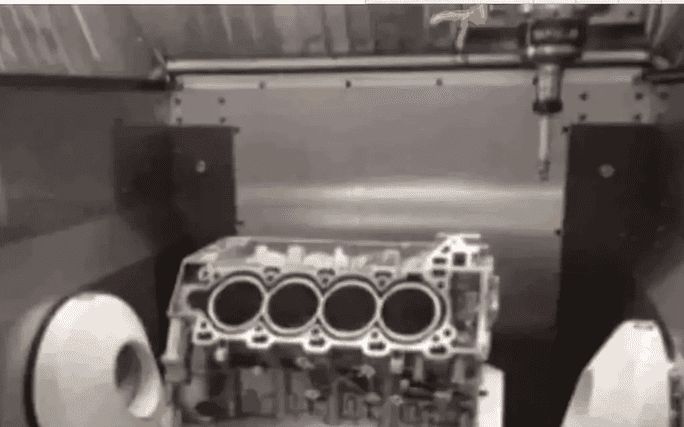
sintering
The sintering furnace can sinter thousands of blades at a time. The blade is heated to about 1500 ℃, in which the process takes about 13 hours, and the pressed powder is melted into cemented carbide, which is an extremely hard material. However, this process will lead to serious shrinkage: the size of the sintered blade is only about half the size of the pressed part. After being sent to the laboratory again for quality inspection, grind the top and bottom of the blade to the correct thickness. Because cemented carbide is very hard, it is necessary to use a grinding wheel containing 150 million small industrial diamond particles to grind it to the correct thickness. Usually, the blade has to be polished again to achieve its accurate groove shape and size.
This is a key step in the manufacturing process. The use of 6-axis grinder can ensure very strict tolerance, so that a joke has been circulating in the factory: “if you sneeze, the tolerance will change immediately”.
Clean and coat the blade immediately after grinding. To avoid any grease or dust, gloves must be worn when taking the blade. There are two different coating methods of blade coating: chemical vapor deposition (CVD) and physical vapor deposition (PVD). In a typical CVD, the blade substrate is contacted with one or more volatile coating gases, which react on the surface of the blade substrate to generate the required deposits. The physical vapor deposition process is carried out in the low-pressure furnace. The blade is placed on the rotary conveyor belt and coated to make the blade harder, stronger and even more wear-resistant.
After this step, the blade can be packed and transported at any time, but a thorough quality inspection must be carried out before shipment. Even if it has been inspected many times in the whole process, manual inspection shall be carried out with the naked eye. In addition, compare with blueprints and batch orders, and mark the correct material with a laser