Physical vapor deposition coating is an advanced surface treatment technology widely used in the world. Its working principle is to use gas discharge to partially ionize the gas or evaporated substance under vacuum conditions, and deposit the evaporated substance or its reactant on the substrate while the gas ions or evaporated substance ions bombard. At present, the most widely used PVD technology in the market is mainly divided into three categories: magnetron sputtering, multi arc ion plating and vapor deposition.
Magnetron sputtering coating of PVD
Working principle: electrons collide with argon atoms in the process of accelerating to the substrate under the action of electric field, ionizing a large number of argon ions and electrons, and electrons fly to the substrate. Argon ions accelerate the bombardment of the target under the action of the electric field, and a large number of target atoms are splashed out and deposited on the surface of the base layer to form a film layer.
Characteristics of sputter coating
(1) small particles
Sputter coating can make the film particles fine, which is suitable for optical grade coating
(2) low deposition rate
Sputtering coating is not suitable for industrial coating because of its low deposition rate and low efficiency
(3) uniform coating
The sputter coating has the characteristics of small particles and slow deposition, and the high-precision coating can be achieved with appropriate loading mode
(4) high binding force
Compared with traditional coating, sputter coating has higher adhesion to substrate
(5)complicated process
Sputtering coating requires higher configuration
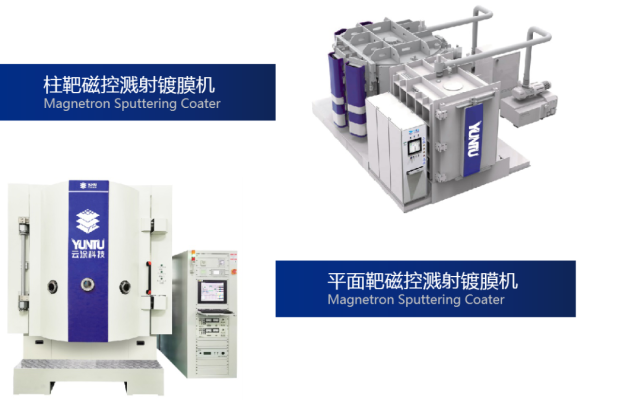
Multi arc ion coating
Working principle: the method of arc discharge is adopted to directly evaporate metal on the solid cathode target. The evaporated material is the ions of the cathode material emitted from the bright point of the cathode arc, and then deposited on the surface of the substrate as a thin film.
By combining glow discharge, plasma technology and vacuum evaporation, ion plating can not only improve the film quality, but also expand the application range of the film.
Characteristics of arc coating
(1) higher production efficiency
(2) the single ion energy of arc coating can make the coating firmly deposited on the substrate surface
(3)?stable process, more accurate control can be achieved on the composite coating
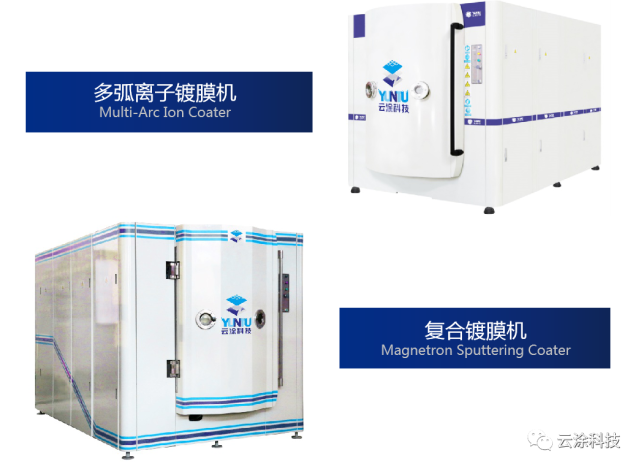
Vapor deposition coating
Working principle: under the vacuum condition, the coating material (or film material) is evaporated and gasified by certain heating and evaporation method, and the particles fly to the surface of the substrate to form a film.
vapor deposition coating’s characteristics
(1) simple process, mature technology and wide application
(2) it is not suitable for high melting point materials and low hardness materials, and it is not suitable for large-scale production because of the slow coating time
Performance of PVD coating
Compared with traditional surface strengthening technologies, such as electroplating, electroless plating and chemical heat treatment, PVD coating has good adhesion performance, good coating quality, wide range of plating materials, and the thickness of the film is micron. Therefore, various physical and chemical properties of the workpiece surface can be improved without affecting the original size of the workpiece. In addition to plating non-metal or metal on metal workpieces, PVD can also be plated with metal or non-metal on non-metal, or even plastic, rubber, quartz, ceramic, etc., to achieve the functions of wear resistance, friction reduction, corrosion prevention, rust prevention, heat resistance and oxidation resistance.
According to many statistics, the use of PVD coated inserts not only reduces the use of release agent, labor cost and mold change time, but also greatly improves the output and yield, providing an effective solution for enterprises to increase efficiency and reduce costs, save energy and reduce pollution.