The engine is responsible for generating the power required for the movement of the vehicle. Nowadays, with the demand of reducing emissions and improving power efficiency, the development of engine is more and more intense.
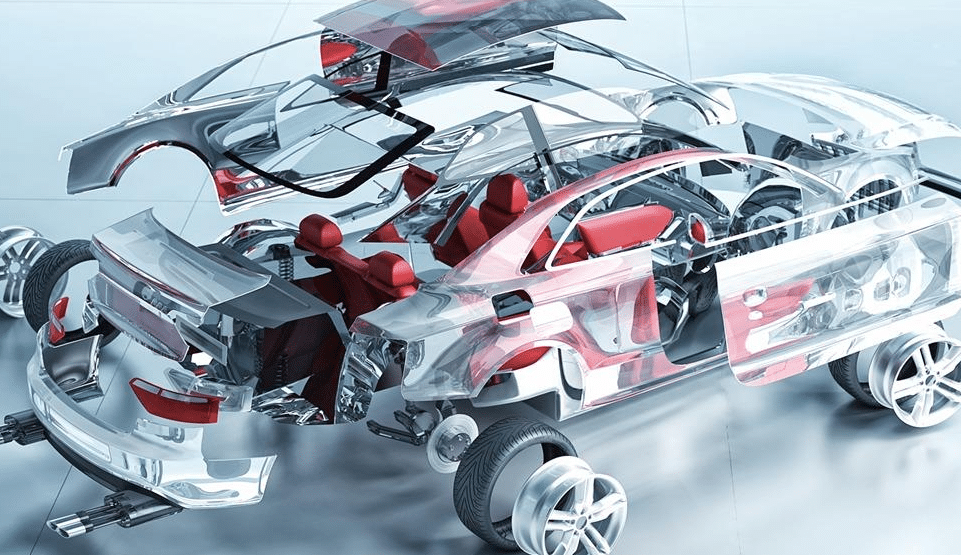
New materials, regulations and other drivers have brought a lot of investment into R & D. The main trend is miniaturization of internal combustion engines to minimize environmental impacts. Another development trend is power train electrification.
TESA precision’s solutions and tools for engine parts are backed by in-depth application of professional technology. With a professional engineering team supporting the automotive industry through a variety of high-quality solutions, we also have a place in the international market. Here, we will share selected high productivity solutions for some of the challenging features of engine parts production.
Cylinder block
The cylinder block is the main structure of the engine, which is the shell of many different moving parts to generate the power required by the vehicle movement.
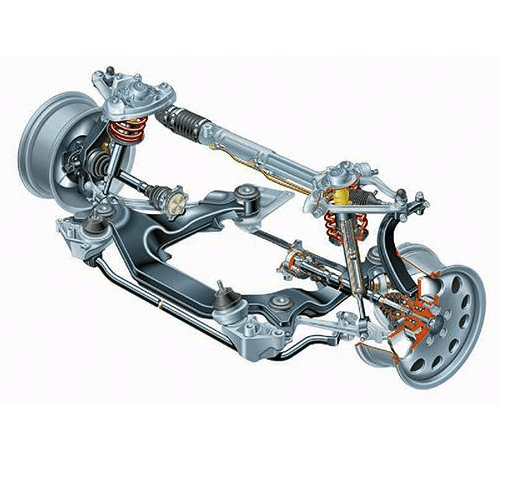
The cylinder block is a part of the main structure of the engine. It is the shell of many different moving parts that generate the power required by the vehicle movement together.
For many years, the engine cylinder block is made of cast iron alloy because of its high strength, low cost and good wear resistance. However, as the engine becomes more and more complex, in order to reduce the weight of the engine and improve the strength and wear resistance, new materials are also put into use. Nowadays, the most commonly used material of passenger car engine is aluminum alloy, which is due to its lighter weight and excellent casting performance. Commercial vehicles will continue to use cast iron, but more high strength alloys.
The manufacturing process of cylinder block involves the most machine tools in the production of automobile parts, as well as several complex processes and strict tolerances. The high quality of cylinder block is very important to the performance of vehicle. For these types of parts, high economy manufacturing is very important.
The cylinder cover
The cylinder head delivers air and fuel to the combustion chamber and covers the cylinder. It is also the shell of many different parts.
The cylinder head is used to deliver air and fuel to the combustion chamber. Because it is located on the top of the cylinder block, it can cover the cylinder. It is also the housing of many different parts such as valves, spark plugs and fuel injectors.
In addition to the cylinder block, the manufacturing process of the cylinder head also involves the machine tool with the largest number of automobile parts. In addition, several complicated processes and tight tolerances are involved, especially when machining valve seat, valve guide and top surface. As the cylinder head is an important part of the engine, its quality is very important for the performance of the vehicle. For these types of parts, high economy manufacturing is also very important.
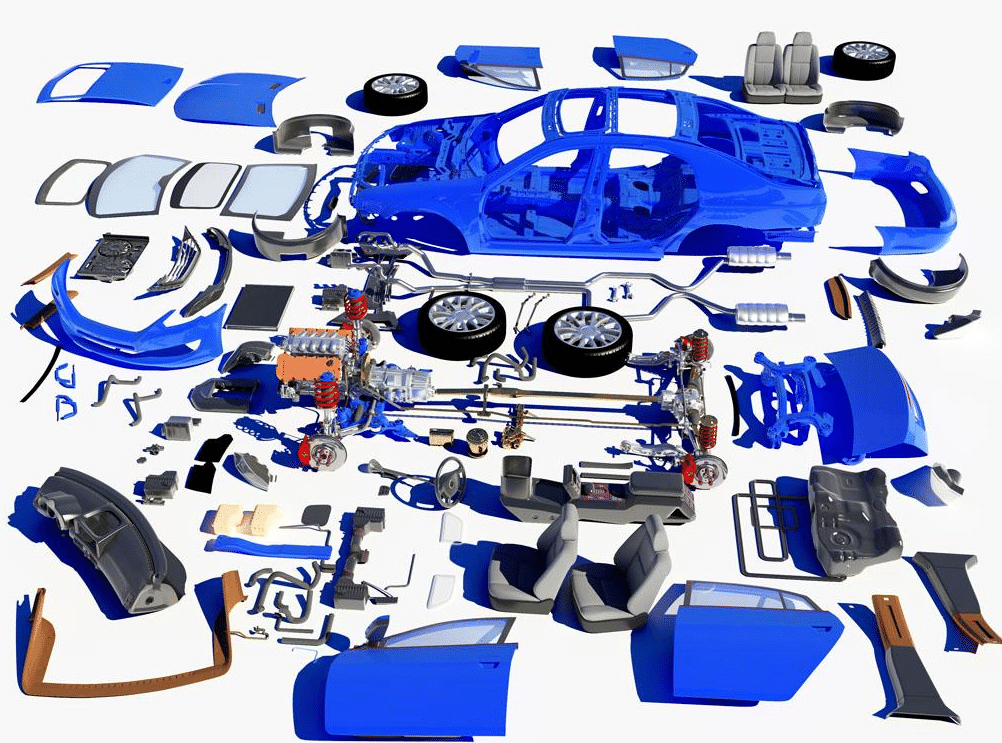
crankshaft
This part is used to convert linear motion and power into rotary motion, so as to make the shaft rotate, so as to make the vehicle move.
Asymmetric and relatively slender crankshafts form the heart of all vehicle internal combustion engines, from motorcycles to heavy trucks. It is also one of the most challenging parts to process. Considering the structure of crankshaft, high tolerance requirements and machining challenging materials (forged steel or nodular cast iron), only the truly optimized tools and methods can be used to process successfully.
Camshaft
The camshaft is used to control the valve operation so that the combustion cycle is synchronized.
In internal combustion engines, camshaft is used to control valve movement and synchronization. It consists of a shaft with multiple lobes and a camshaft for each valve. When the cam blade rotates, it exerts pressure on the valve (or some intermediate mechanism) to force the valve to open.
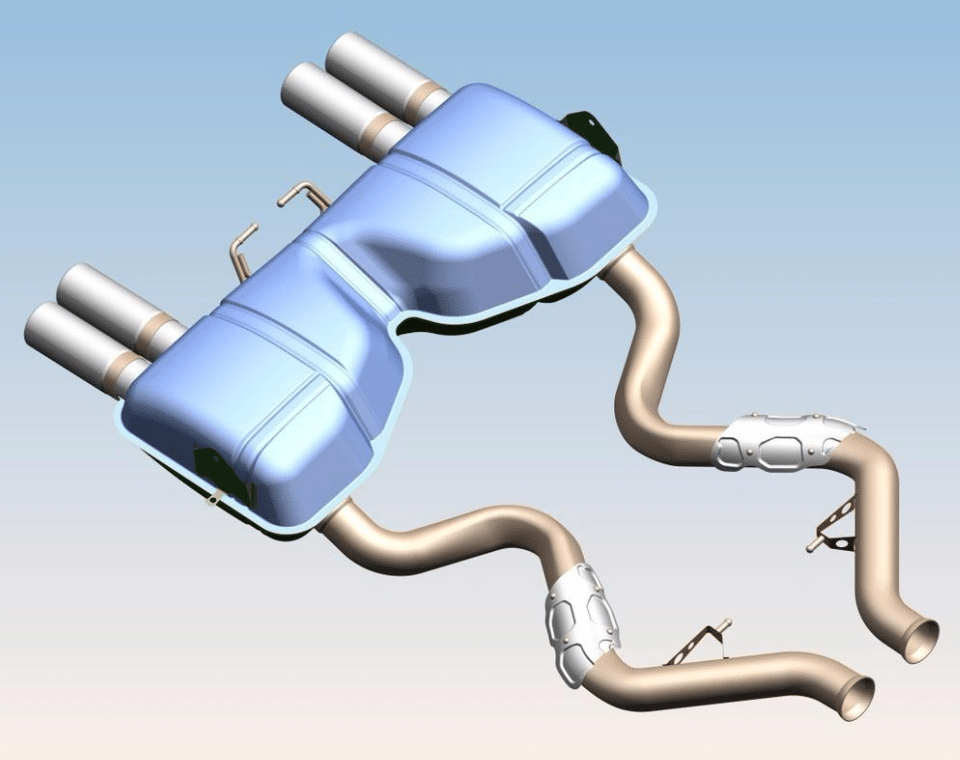
connecting rod
The connecting rod is used to transmit linear motion from the piston to rotate the crankshaft.
The connecting rod is used to transmit linear motion from the piston to rotate the crankshaft. It is under the huge stress produced by the reciprocating load, and it will be stretched and compressed every time it rotates. The reciprocating load increases squarely with the increase of engine speed. Different from the early methods of cutting with milling cutter, the big end is usually processed by pyrolysis. When cracking the big end, it may be necessary to pre process a laser crack, which will put forward high requirements for the subsequent boring process.
The manufacturing process of connecting rod must be precise in terms of important tolerance and high economy at the same time.
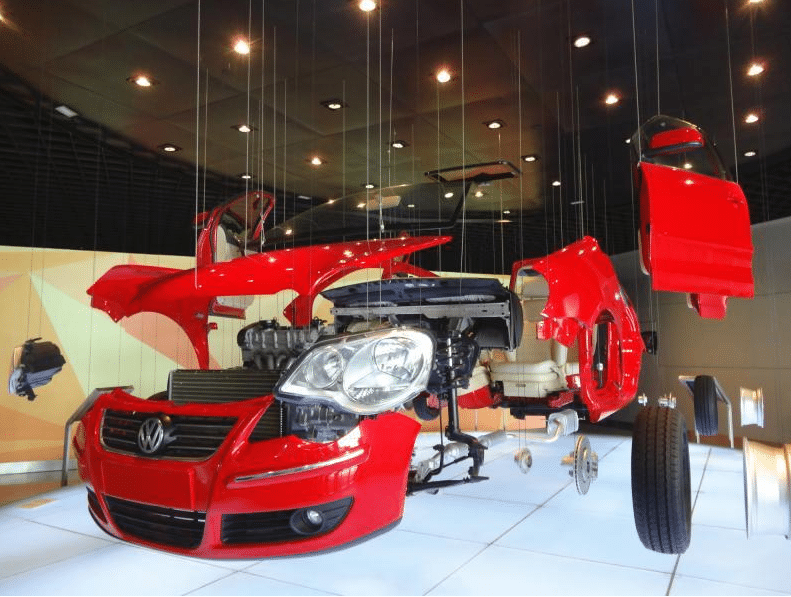